1970年代のラベラーの動向
まず1970年代の国内外のラベラーの動向について述べる。
国内では、澁谷工業が1969年に英国モルガンフェアレスト社とラベラーでの技術提携を行い、海外技術の導入による生産を開始した。海外では、クロネス社が1970年に糊付けラベル取り出し方式のラベル供給ステーション(枚葉ラベル)を開発し(以下図)、B&H社がロールラベラーを導入(以下写真)、Accraply社がタックラベラーを出荷している。
国内のラベラーに関係する動きでは、1972年にリンテックがタックラベラーの製造・販売を開始し、三晴精機が口紅用タックラベラーを販売している。1973年にはイーデーエムがタックラベラー「LM-200型」を開発し、大阪シーリング印刷がタックラベラーを発売している。1976年にはシーレックスがKugler-Womako社のタックラベラーを製造・販売する。
国内の企業では自力での独自ラベラーの開発は行われず、海外からの技術導入によって製品を生産していた。
以上のように、独自開発か否かに関わらずこの時期には国内外で現在ラベラーにかかわる企業が続々と参入してきたことがわかる。振り返れば、まさに百花繚乱という様相であった。
国内では、その機種の多くがタックラベラーであり、独自のラベラー技術は限られたものであった。なかでも注目すべきは、1970年に当社と同じくB&H社がロールラベラーを開発・販売し始めたことである。詳細は不明だが、驚くことに吸引式ドラム、スターホイールとスターガイドやR仕上板の使用など共通点がみられる。この会社は、現在に至るまでロールラベラーのみで2000台を出荷している。
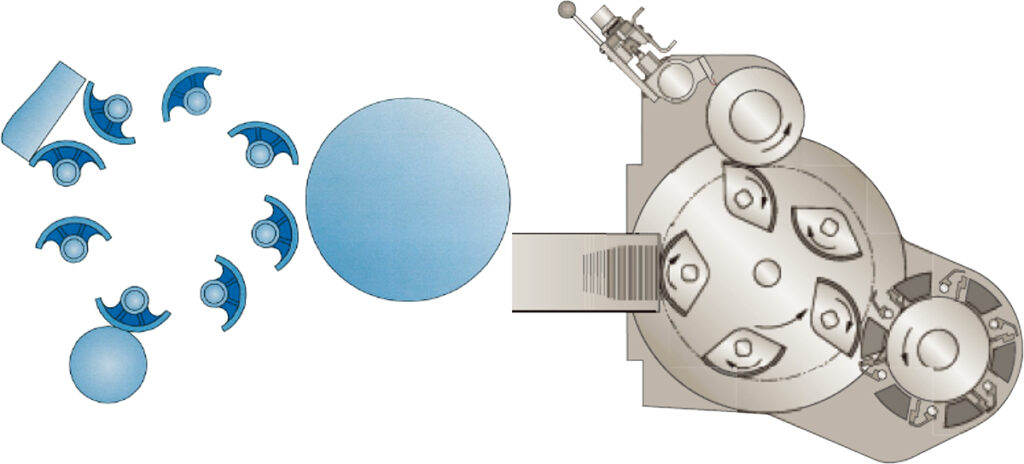
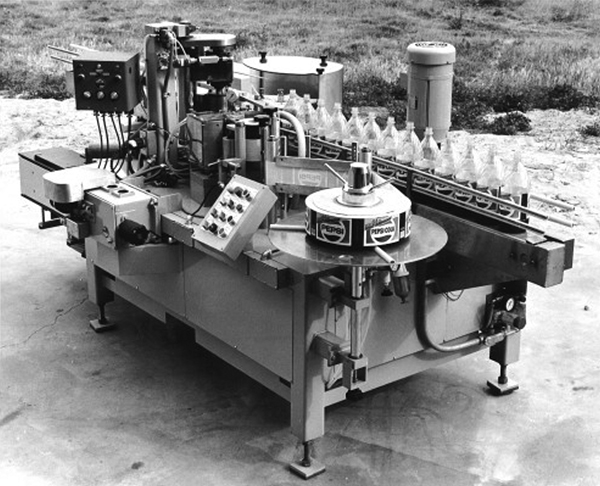
ロールラベラーの開発
こうした動きの中で、当社ではホッパーラベラーの各機種(「LN-305」「LK-300」「KL-KO」「LRW」)が次々と開発され、出荷台数を急速に伸ばしていた。それにもかかわらず、これまでのラベラーの概念を根本的に覆す発想からロールラベラーの開発が進められた(以下写真、図)。
開発を始めた時期については不明だが、ロールラベラーに関係する特許出願は1974年に始まっている。その重要な構成要素であるラベルカッターとラベル送り装置について、固定刃・回転刃式ロータリーカッター(特願1974.8)と、2クランク間欠ラベル送り機構(特許1974.11)の特許出願が相次いでみられる。後者はその翌年に、米国とフランス、イギリスでもそれぞれ特許出願(米・英・仏、特許1975) し登録されている。
1975年(昭和50年)には、間欠ラベル送り式ロールラベラーの1号機「LRY-2000(G社)」を世に送り出している。
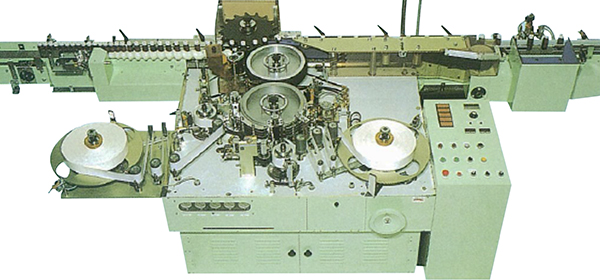

ロールラベラーの優位性
異種ラベルの混入を防ぐ
ロールラベラーの第1の優位性は、異種ラベルの混入を防ぐことにある。すなわち枚葉ラベラー(ホッパーラベラー)では、大量の枚葉ラベル(カットラベル)をホッパーにセットする際に、異種ラベルが混入する可能性がある。ロールラベラーでは、未切断のロール状に巻いたラベルを容器に貼り付ける寸前に切断することで、異種ラベルの混入はありえない。これにより、ラベルの管理が容易になり、人為的ミスを事前に防ぐことになる。
生産の高速化を先導する
第2の優位性は、高速運転に対応できることにある。
ラベル貼付能力は、枚葉ラベラー(ホッパーラベラー)では毎分150本程度が限界であるの対し、ロールラベラーでは毎分200~800 本まで可能であり、現在では最高毎分1500本という能力まで達している。なんと毎秒25本の容器にラベルを貼り付けるという能力である。
生産コストの削減
第3の優位性は、高速化や省エネによる生産コストの削減に止まらず、ラベルコストを大幅に削減することである。
枚葉(カット)ラベルは、ロールラベルより単価が高い。ラベルをカットして揃えセットするという生産工程を経て初めてラベルになる。それに対してロールラベルは、紙であれフィルムであれ、原反に直接印刷して巻き取ることでラベルが完成する。そのため1枚あたりの単価は、ロールラベルの方が格段に安価である。
ロールラベラーの中核技術
ラベル送り機構
まず第1に挙げられる中核技術は、ラベル送り機構にある。
ラベル送りの成否は、一定ピッチに印刷されたロールラベルを如何にして、印刷ピッチに合わせて送り出しカットするかに掛っている。そのため、ロールラベルに印刷されたラベルマークをセンサーで随時検出し、その信号をフィードバックしてラベル送りの微妙な誤差調整をその都度行わなければならない。つまり印刷ピッチに合わせてわずかに送りを大きくしたり小さくしたりする。ここが革新的な技術である。
サーボ制御装置が存在しなかった当時に、ラベルマークを検出してクラッチ切り替えによって、ラベル送り量の自動制御をメカニカルに実現したのである。
ラベル張力調整機構
第2にはラベル張力調整機構である。ロールラベルの送りに伴う張力の変動を如何に低減するかということだ。
ラベルテーブルにセットされたロールの慣性のため、ラベル送り速度の急変によって張力が大きく変化する。そのためラベルの伸張によって送りに誤差を生じたり、場合によってはラベルが破断する原因となる。
これをラベルテーブルに付随して設置された、テンションローラーアームの動きに対応したブレーキ機構によってメカニカルな仕組みで解決した。
ラベルカット機構
第3はラベルカット機構である。高速のラベル送りに対応可能で、運転のエネルギー損失が小さくカッター刃の切れ味が落ちにくい。かつ膨大な切断回数に耐えうるラベルカット装置を如何に実現するかということである。
これは、「鋏切り」という固定刃・回転刃式ロータリーカッターによって解決している。
ラベルカット機構―固定刃・回転刃式ロータリーカッター
ロータリーカッターは現在、採用されている固定刃可動式ロータリーカッター以前の方式である。
ロータリーカッターの各構成要素は、すでにこの最初の段階で完成されたものとなっている。この方式は開発されて以来長い間、ロールラベラーのロータリーカッターとして採用されてきた(以下写真)。このロータリーカッターについは、特願「テープ等の切断機」(出願1974.8)に詳述されている。最大の特徴は、回転刃ドラムに回転刃をわずかに傾斜させて取り付けている点である。これは、いわば紙をハサミで切るようにして、ロールラベルを切断しようというものである(以下図)。
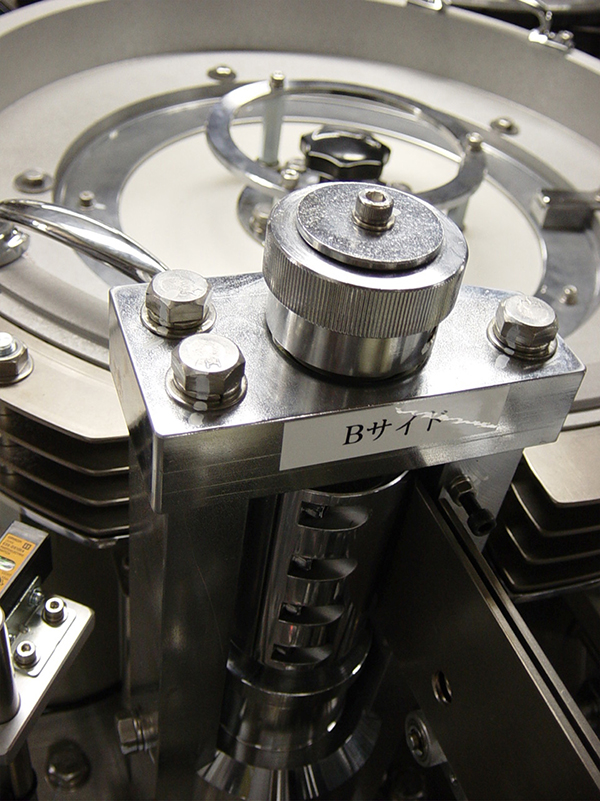
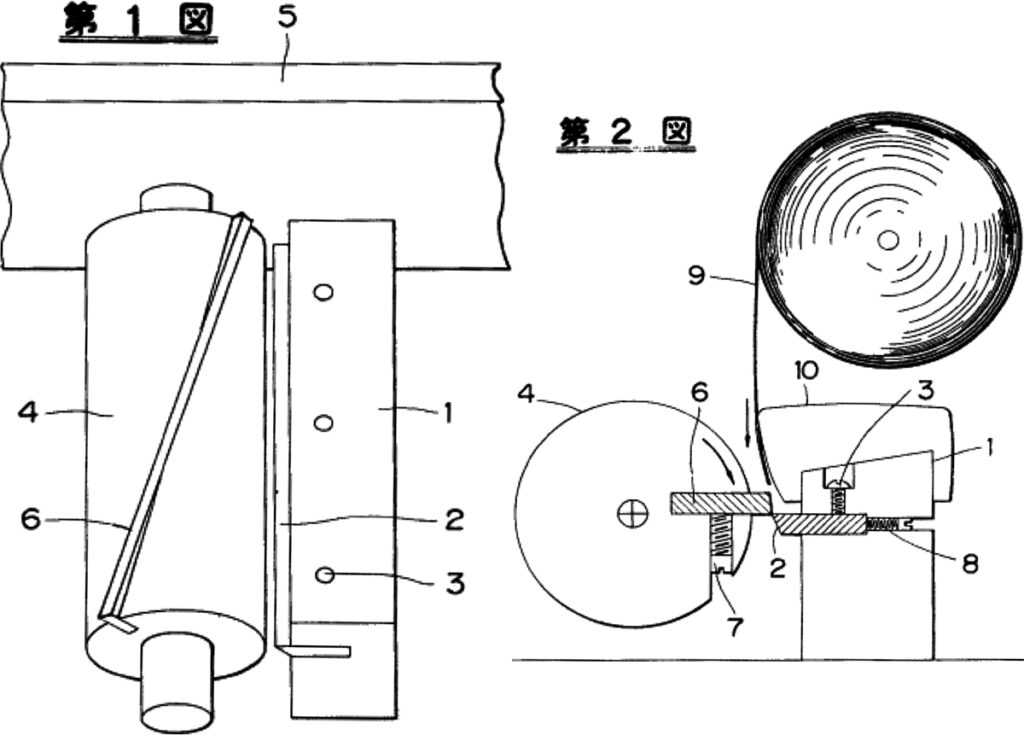
ラベル送り機構一間欠ラベル送り方式
一方向クラッチ式2クランク間欠ロールラベル送り機構(特許1974.11)(米・英・仏、特許1975)
ラベル送り機構の最初の特許である特許「テープ送り装置」(出願1974.11)に、そのメカニズムが詳述されている。ラベル送り機構は間欠ラベル送り方式である。ロールラベルを高速度で送り出し、低速度送り出しに切り替えて停止するという動作を繰り返す。そのラベル送り停止時にロールラベルをロータリーカッターで切断する。そのためカット精度は、ラベル送りの停止位置の精度にかかっている。この機構を一言で表現すれば、「一方向クラッチ式2クランク間欠ロールラベル送り機構」となる。
ロータリーカッターと一方向クラッチ式2クランク間欠ラベル送り機構の開発によって一応の完成をみた。だが、その後も市場のニーズを先取りしながら、より高速なラベル送りとカット精度の向上を目指し、新たなラベル送り機構の発想やクランク式ラベル送り機構の改良が進められた。
ラチェット式間欠送り機構(特願1979.6)
さらに新たな間欠送り機構を、回転盤に刻まれたラチェット歯にラチェットストッパーの爪が掛かることによって確立したもの。その最終停止位置の精度を高めるために、ラチェット歯に3個のストッパー爪の内1個だけ掛かる(歯のピッチの3分の1の精度)ようにし、遥動リングと遥動装置により停止と解除を行っている。
過回転防止機構付き一方向クラッチ式2クランク間欠送り機構(特許1979.7)
間欠ラベル送りの高速化を目指して考案されたもので、前述の「一方向クラッチ式2クランク間欠ロールラベル送り機構」の改良型である(以下図1枚目)。
ラベルのカット精度は、ラベル1枚当たりの送り出し量の精度によって決まる。すなわち、間欠ラベル送りでは、その停止位置の精度がその成否を握っている。より高速なラベル送りでは、重量のあるドラム(D)の慣性力により停止位置がズレることがある。これを防ぐために主クラッチ(5)の直下に一方向クラッチ式過回転防止装置を搭載している。
高速送り停止装置、解除クランク付き一方向クラッチ式3クランク間欠送り機構(特許1979.11)(米国特許1980)
さらなる間欠ラベル送りの高速化を目指し、改良を重ねて行く中で到達した最終版の機構を記述している(以下図2枚目)。
より高速な間欠ラベル送りでは、上述の一方向クラッチ式過回転防止装置(10)が機能してもわずかに停止位置がズレることがあった。その過回転防止装置をわずかな時間差で解除させる解除クランク(123)を装備することによって、間欠ラベル送りの停止精度が更に向上したのである。
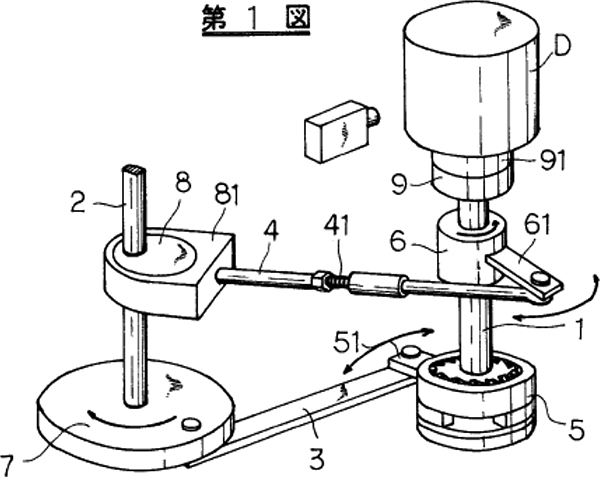
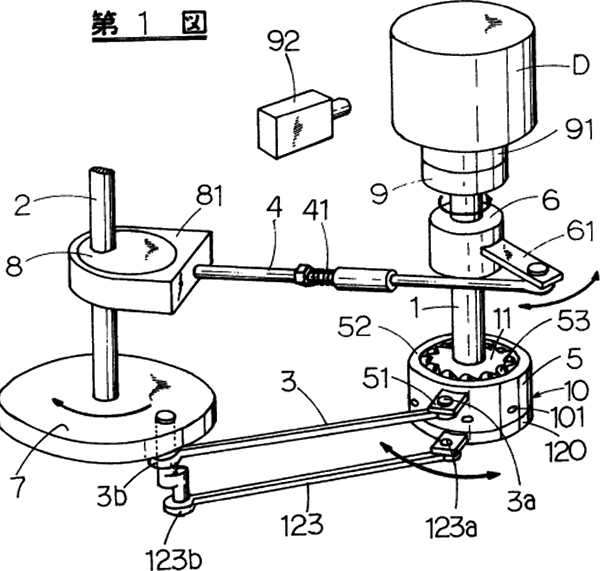
ラベル張力調整機構
ラベル張力調整機構について述べる。ラベル張力の変動を低減するには、ラベル送り装置による引き出し量と同調して送り出すか、一定の張力に保ったままラベルが引き出さなければならない。すなわち、前者はラベル引き出し量と同調して駆動ラベルテーブルがラベルを送り出す。この場合、ラベルロールはラベルが供給されていくに従いロール径が減少していくため、減少に応じてラベルテーブルの回転速度を徐々に大きくする必要がある。後者は、フリーのラベルテーブルから一定の張力を保ったままラベルを引き出す。この場合、ラベル引き出し速度の変化に応じて、ラベルテーブルの慣性力による回転をコントロールしなければならない。
回転駆動制御式ラベルテーブル(特許1975.12)
前者の駆動ラベルテーブルによってラベルを送り出す方式を示している(以下図)。
ラベルが供給されロール径が減少し、ロール(4)外面とセンサー(61)との距離が一定値に達すると信号を発信する。その信号により電磁ブレーキ(6)が解除され検出アーム(13)がラベルロール側へ振れ、駆動テーブル(4)に接する駆動輪(41)が内側に移動する。そのためにラベルテーブルの回転が増速することになり、送り出される長さが一定に保たれる。
この特許で示されている内容は、現在使用されているサーボモーターによるラベル送り出し制御に通じる。
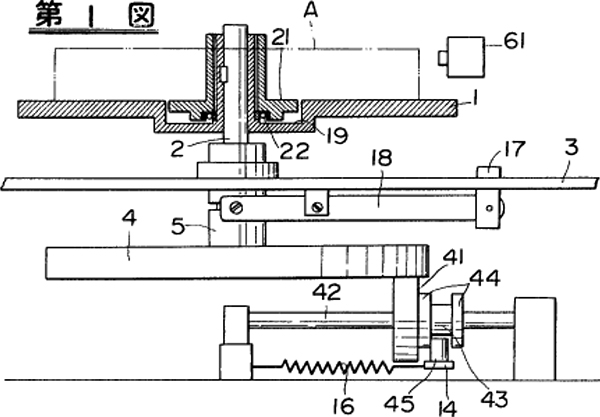
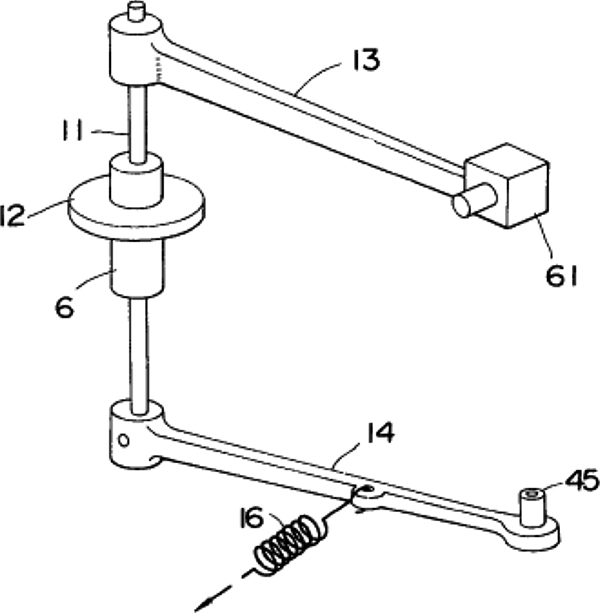
テンションアーム式ラベルテーブル(特願1980.8)
フリーのラベルテーブルから引き出される張力の変動をコントロールする機構を示している(以下図、写真)。
ロールラベル(R)の張力の増減によってガイドローラー(2)のテンションアーム(21)は首振り運動をする。その動きに連動して、摩擦円盤(12)へ制動用シュー(3)の接したり離れたりさせて、ラベルテーブルの回転速度を制御する。すなわちラベル張力が増して、テンションアームがラベルテーブル側へ振れると、制動用シューが摩擦円盤に接触してラベルテーブルにブレーキをかけて減速させる。逆にラベル張力が減って、テンションアームがラベルテーブルから離れる方向に振れるとブレーキが解除される。この動作が瞬時に繰り返されて、ラベル張力の変動を制御するのである。
旧型ロールラベラーに長い間、この機構が採用されてきた。その後も、ラベル送り機構やラベル張力調整機構、ラベルカット機構といったロールラベラーの中核技術は、弛まぬ開発・改良が進められた。
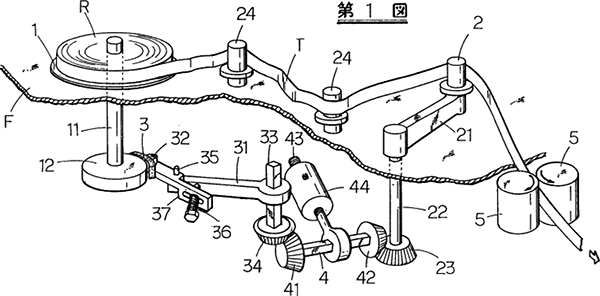
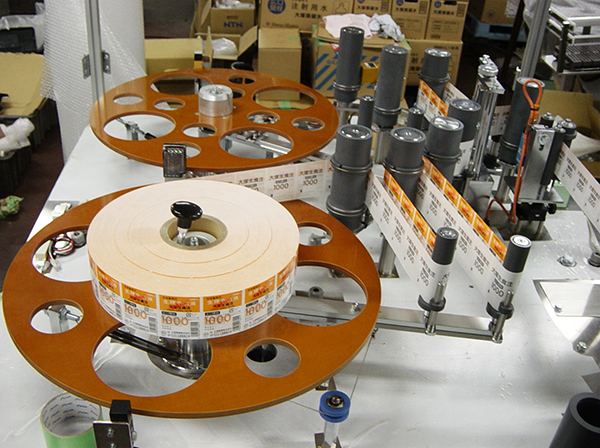
ロールラベラーの普及
その当時(1974年)は、ラベルメーカーではロールラベルを生産しておらず、ロールラベル自体が無い状況にあった。そのためロールラベル用の印刷機械も製作しなければならなかったようだ。さらにロール紙に印刷を施したロールラベルを紙管に巻きつけてラベルロールを作り上げるわけである。
こうした努力によって、少なくとも日本で初めてロールラベルが誕生したわけである。それでも、なかなかロールラベラーの普及には時間を要したようである。逆にロールラベルの印刷方法をラベルメーカーに教え、ロールラベラーのすばらしさをラベルメーカーにアピールしたというエピソードも残っている。
そうしてラベルメーカーとともに努力して販売ルートができ、ロールラベラーの普及が進んだのである。