製薬企業から要請を受け、目薬容器や注射器にシュリンクタックラベルを巻き付けて熱収縮させ、凹凸のある容器に密着させる、シュリンクタックラベラーの開発に着手することになる。
シュリンクタックラベラーは、製薬企業S社の目薬容器用として初めて開発され1993年に納入された。そのシュリンクタックラベルは、丸胴の目薬容器のキャップまで覆うもので、キャップ部がテーパーしている。従来方法である貼付ドラムとR仕上板で貼り付けられ、通常のコンベア上で熱風によって収縮させて密着させるものであった。その後、他の製薬企業C社から要請され、初めて注射器用シュリンクタックラベラーとして開発し、1999年に出荷している。注射器は鉛直に立った姿勢で貼付スターホイールを回転搬送されながらシュリンクタックを貼り付け、鉛直コンベア搬送で熱風を吹き付けて収縮させるという方式である。
シュリンクタックラベラーの確立
さらに窪みのある不定形の目薬容器用のシュリンクタックラベラーが開発され、製薬企業S社に2001年に出荷している。不定形容器に全体を包み込み、しかもキャップ部分のラベルを剥すために容器天面に「つまみ」が付いたラベルであった。このシュリンクタックラベラーには、いくつかの困難な課題があった。
第1には目薬容器が円筒状の丸胴でないこと、第2にはラベルがキャップ天面までオーバーラップすることである。よって、これまでの方法ではラベルを貼り付けることができないのである。それを克服するには、ターレットロータリーで容器を回転搬送している間に、不定形キャップ部に中空のボビンを差し込んで丸胴部を作る必要があった。すなわち貼付けロータリ一部で、容器と同じ径の非着処理したボビンで容器の変形頭部に被い押さえ付け、その状態で容器とボビンを一体化してシュリンクタックラベルを捲いて貼り付けるのである(以下写真、図)。
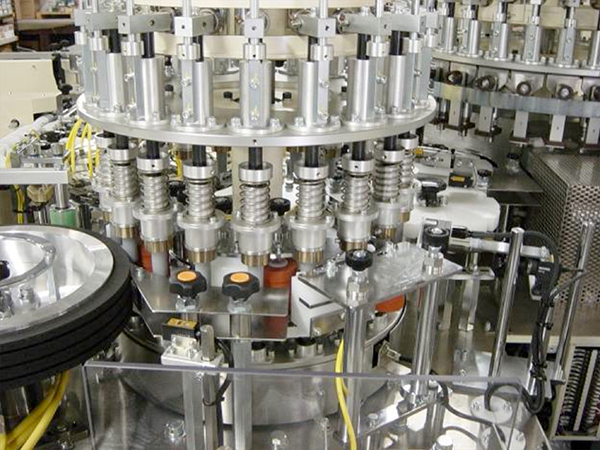
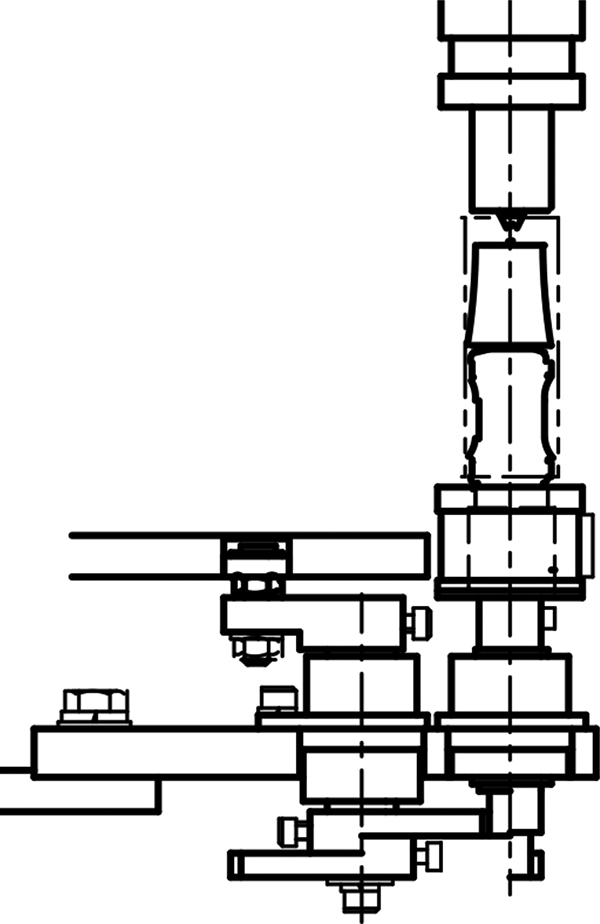
その後の工程である熱収縮ロータリ一部で、ボビンを引き抜いた状態で容器の頭部を押さえつけながら、熱風を吹き付けてタックラベルを収縮させて容器に密着させる(以下写真1枚目)。
第3には、窪みのある不定形容器の向きとラベルの向きを合わせる必要があったのである。ラベルを貼り付ける際には、容器の向きが揃っている必要があり、ラベルを貼り着ける前に方向規制を行わなければならない。先に述べた特許「窪み付き軽量容器の方向規制装置」の技術によって、この課題は克服された(以下写真2枚目)。
この新たなシュリンクタックラベラーの完成によって顧客メーカーの信頼を獲得し、同じ製薬メーカーに同じ機種のシュリンクタックラベラー6台を収めることになる。また同機種は、他の国内製薬メーカーにも出荷されたり、海外の製薬メーカーにも輸出されたりして好評を博している。
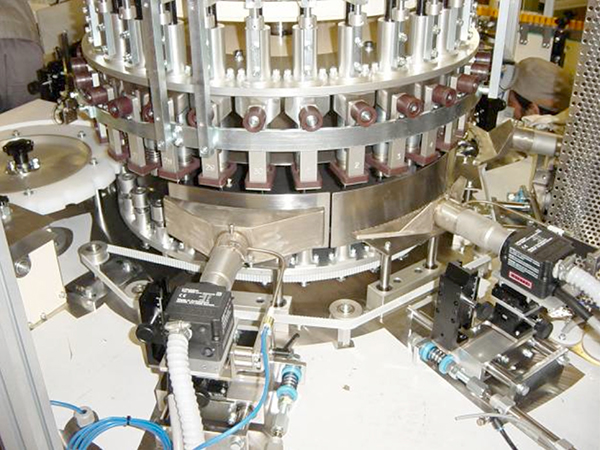
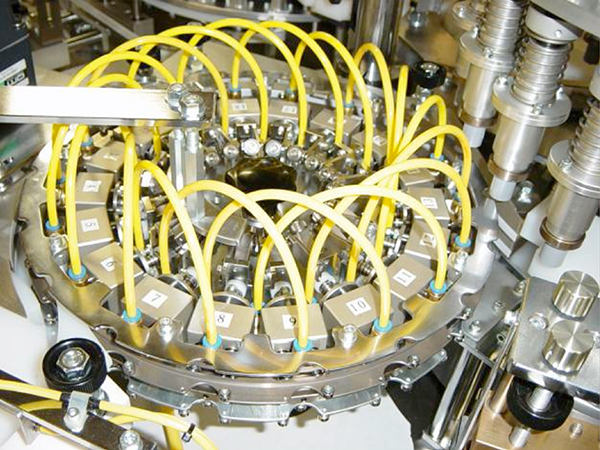
テープ状ラベルから筒状シュリンクラベルヘの技術的背景
ここで使用されている技術は、テープ状のラベルを筒状のラベルに成形するために開発されたものである。
そもそもシュリンクラベラーは、あらかじめ筒状に成形されたシュリンクラベルを容器に装着し、加熱してラベルを収縮させてその形状に合わせて密着させるものである。その筒状のシュリンクラベルは、テープ状のロールラベルに比べてかなり高価である。シュリンクラベラーに、テープ状のラベルを筒状ラベルに成形する工程を加えることで、累積コストが膨大になるラベルコストを大幅に削減することができる。その筒状のラベルを成形する装置を搭載したラベラーの価格が多少高くなったとしても、そのラベラー購入のイニシャルコストは、筒状のラベルとテープ状のラベルとの累積差額で、1年ほどで相殺されてしまう。
以下に、筒状ラベル形成の特許の概要について記しておく。
可動ボビン式筒状ラベル形成シュリンクラベラー(特許1999.6)
可動ボビンに容器の頭部に挿入し、ボビンと容器にテープ状のラベルを巻き付けて接合して筒状のシュリンクラベルを形成する。
次に筒状のシュリンクラベルを押さえて可動ボビンを抜き取り、加熱してシュリンクフィルムを収縮させ容器に密着させる。これによりラベルコストを大幅に低減化し、ラベル貼付の高速化が図れる(以下図1枚目)。
筒状シュリンクラベル形成挿入装置(特願2000.2)
成形ボビンにテープ状のシュリンクラベルを巻き付けて接合して筒状のシュリンクラベルを形成し、その筒状のシュリンクラベルを下げて容器に挿入する。その後、加熱してフィルムを収縮させ容器に密着させる。これによりラベルコストを大幅に低減化するとともに、容器のリサイクルに貢献することになる(以下図2枚目)。
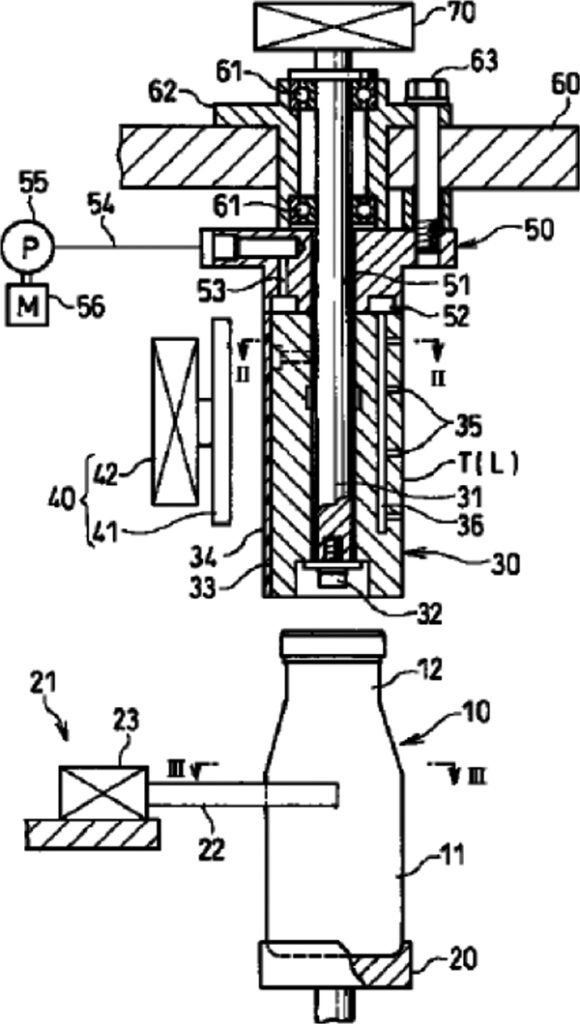
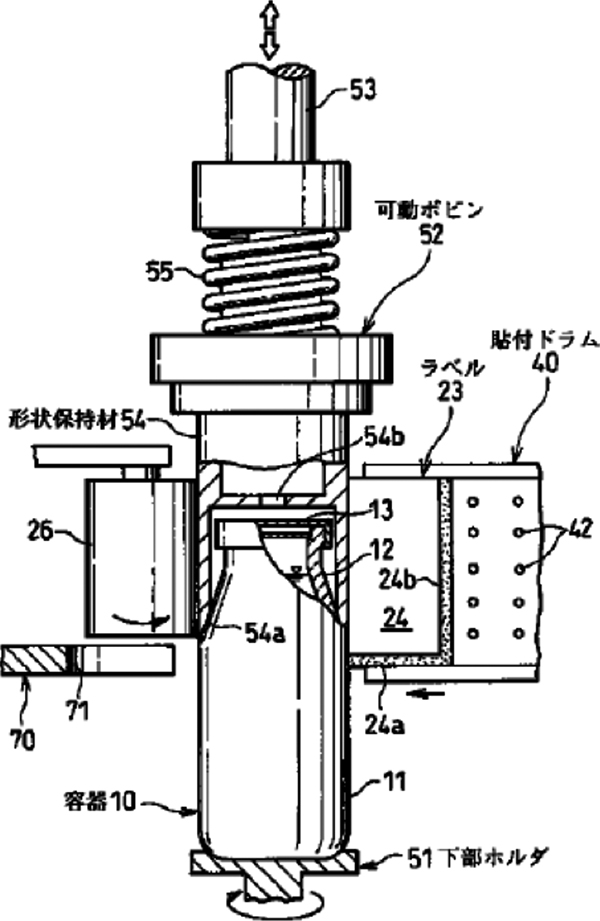
タックラベラー複合機や周辺機器
近年タックラベラーは、製薬企業への納品が大きな割合を占めている。タックラベラーと他の装置との複合機や、タックラベラー前後の周辺機器と合わせてラインを一括して納入する場合がある。例えば容器にタックラベルだけでなく、シュリンクラベルや国家検定証紙を貼り付けるラベラーとの複合機である。あるいは、容器にタックラベルを貼り付けた後に容器を整列させて集積し、トレー詰めする集積装置を備えることもある。
さらに、タックラベラーの前後に、製品の外観検査装置やラベル貼付検査装置を備えた複合機である場合もある。それらの代表例について、以下に紹介する。
タックラベラーとシュリンクラベラーとの複合機
不定形の目薬容器には筒状のシュリンクラベルを挿入し、熱風をかけて仮収縮させる。丸胴のバイアル瓶にはタックラベルを貼り付ける。異なる容器によって、異なる仕様のラベルを貼り付ける兼用型複合機である(以下写真)。
このような複合機にすることで、別々に独立して製作して設置するのに比べ、スペースやコストを抑えてかつライン制御の複雑化を避けることもできる。
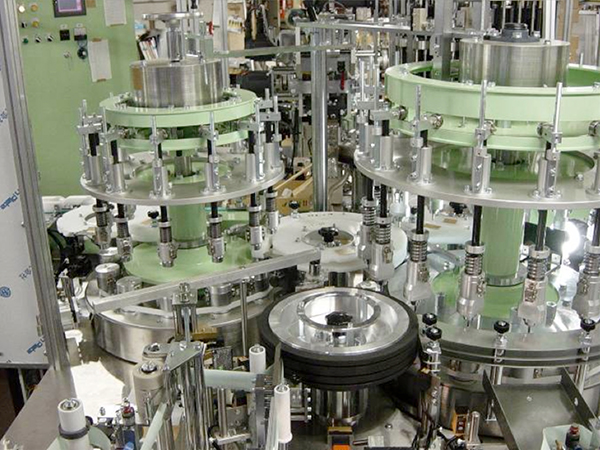
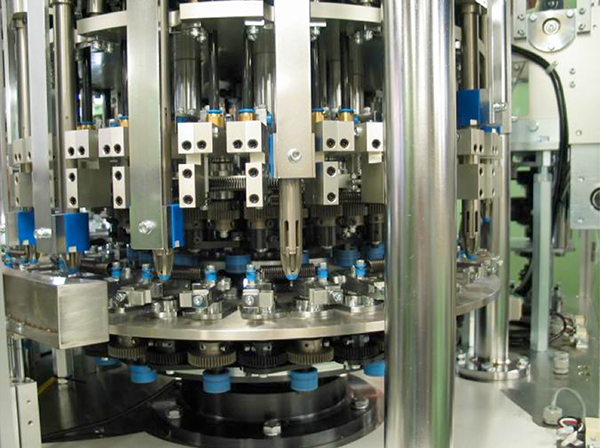
注射器組立とタックラベラーとの複合機
注射器組立機は、薬液充填の注射器のバレル部にプランジャロッドを装着してガスケットに巻き締めて組み込み、バックストップを装着して注射器を完成させる。各工程後にそれぞれ検査カメラで撮影されて検査し、不良品はラベリング前に排出される。その後に、タックラベラーが注射器のバレル部にラベルを貼り付け、ラベル貼付の検査を行い不良品は排出される。注射器組立機の前工程として、プランジャロッド供給機とバックストップ供給機を備える。
このように、多数の工程と複雑な制御で構成される複合機を、機械と制御の両面から一括して設計することで、最小のスペースと系統的な制御で効率的にこなすことができることになる。薬液の充填や栓締めを除いて、当社の複合機はラベリング前後の製造ラインの主要工程を担っている。この複合機の1号機は、2009年1月に製薬企業に出荷されている。
外観検査・ラベル貼付検査とタックラベラーとの複合機
これは、薬液が充填された注射器のバレルを、多面的に検査するシステムを備えた比較的規模の大きな検査タックラベラー複合機である。ラベリングする前に、外観検査ロータリ一部でバレルを回転搬送しながら自転させ、これに同調して遥動運動する検査カメラによって、個々のバレルの内部の液部や空部、ピストン部などを検査する。ラベル貼付ロータリ一部で、バレル部にタックラベルを貼り付けた直後に、ラベルの貼り付け状態を外観検査ロータリ一部と同様なシステムで検査する。さらに各スターホイールでキャップ部の天面や側面を検査カメラにより撮影して検査する。良品バレルは次工程のラインコンベアヘ搬送され、それぞれの不良バレルは不良事項にしたがって分別されて各排出テーブルに排出される。
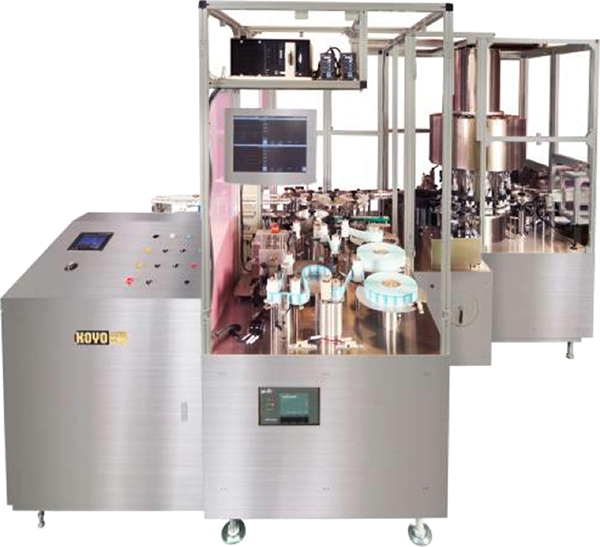
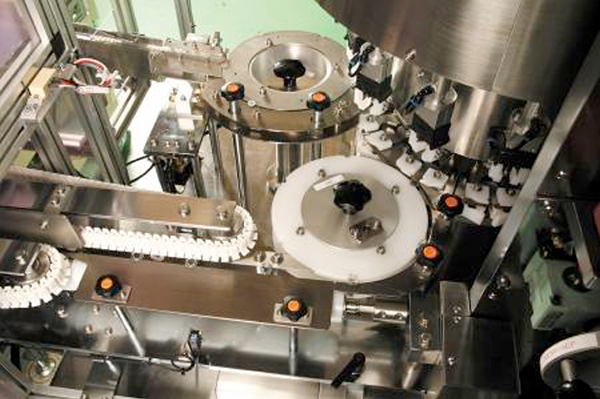
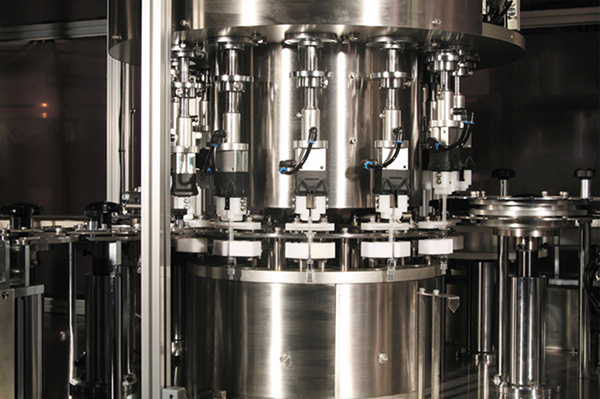
側面/天面貼りタックラベラー複合機と集積装置
各装置がコンベアによって連結されたラインは、容器の供給から始まって容器の側面と天面にラベリングし、ラベル貼付容器を集積してトレーに収納し、搬出されるまでの工程で終結する。タックラベルを貼り付け検査された最終製品の容器は、集積装置内に搬送され一定数ごとに整列させトレーヘ収納し完了するとコンベアにより搬出される(以下写真、図)。
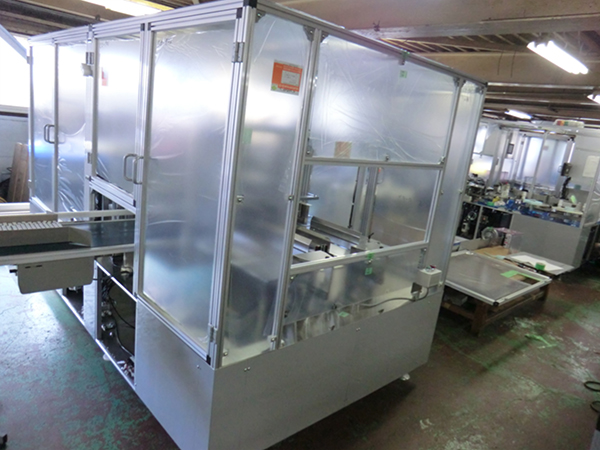
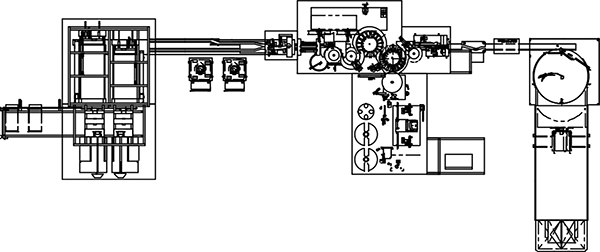
当社は、社会(企業)が求めるものを先取りし、これまで世界になかった技術を独創して新しいラベリングシンを世に送り出してきた。コストの低減や省力化、省エネ化を図る生産ラインに組み込まれる機械設備として、その需要を生み出してきたといえる。
振り返ってみれば、当社の原点であるホッパーラベラーに始まってロールラベラーヘと発展し、タックラベラーへと進出し、ラベリングマシンという範疇の全体像を書き換えている。一方、「ユニークな形状の容器に、斬新なデザインのラベルを貼り付けられないか」という顧客の求めに応えるために、様々な新しい技術を発想し具体化してきたともいえる。機械メーカーとして設計を貫く根本思想とコア技術をベースとし、様々な顧客の要求と先導的な技術との相互作用により、次々にラベラーの技術を進化させてきたのである。その先駆者である山下会長の思想と技術が継承される中で、当社の機械設計技術者や機械組立調整技術者、電気制御技術者の中から絶え間なく、新しい技術の導入や開発がなされ製品化されてきたのである。納品される前の機械調整で、あるいは現地工場での生産立会いのライン運転で機械稼動で明らかになる情報を機械設計・電気設計にフィードバックし、機械装置や制御方法の改良が進められている。それが新しい技術が生まれる原動力となってきたことは言うまでもない。24時間稼働する条件の中で明らかになる機械装置の耐久性、あるいは高い品質基準をクリアする機械装置の精密性や機能性、機械装置の進歩は、まさしく“現場”に始まって“現場”に帰るという繰り返しによるものである。
これまでも述べてきたように、困難な課題であればあるほど、これまでの技術を捨て去るような、よりシンプルで革新的な技術が生まれてきた。また、コスト削減を徹底すると逆に高性能な製品を生み出すことにもなったわけである。様々な分野でかつてない大きな時代変革の時を迎え、これまでにない課題が山積する中だからこそ、当社は新たなラベリングマシンの開発に挑戦していきたいと考えている。それが光洋の“ラベリングマシンの系譜”そのものであるからである。