1980年にはすでに、タックラベラー分野には多くのメーカーが参入し、定式化されたラベリングマシンとして確立されていた。それらは、台紙からタックラベルを剥がす剥離装置から直に、容器へタックラベルを貼り付けるという方式で、ハンドタックラベラーやユニット化したタックラベラーというものであった。ラベル供給や容器搬送が間欠動作であり、貼り付け精度や能力はそれほど高くなかった。そうした状況の中で、本格的な生産ラインに組み込まれるタックラベラーの開発が求められていたのである。
当社では、これまでのロールラベラー技術を生かす方式を模索しながら開発を進めていた。そして1982年に1号機を出荷し、タックラベラーの分野に進出することになる。それは“連続ラベル送り方式”で夕ックラベルを剥離させ、“真空吸引式ドラム”で吸って回転移送し、容器に貼り付けるというものである。この方式によって、ラベルの貼り付け精度や速度は格段に向上させることができた。この開発によって、ホッパーラベラーとロールラベラーとを合わせてラベラーの主要機種が揃うこととなった。
その後、タックラベラーは様々な新技術の導入や新機能の搭載により、主力製品の1つとして成長していくことになる。
なぜドラムを介してラベルに貼り付けるのか?
従来のタックラベラーで、直接に容器にラベルを貼り付けることができるのに、なぜわざわざドラムを介して貼り付ける方式をとったのか。またドラムを装備することでコスト高になるのではないかと思われるであろう。そこで、まずタックラベラーでのドラムの有効性について検討してみたい。ラベル剥離ガイドは、ドラム周面に触れない程度に近接して設置されている(以下図)。
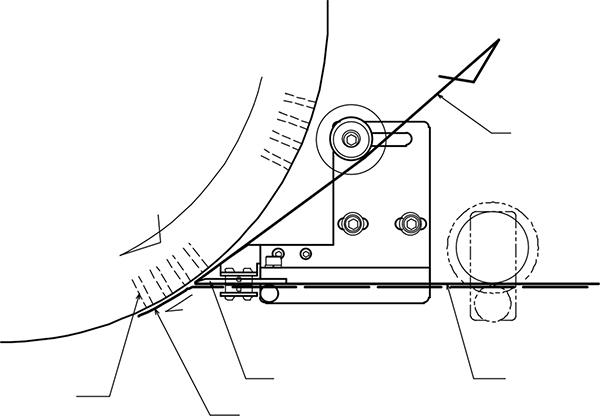
そのため、ラベル剥離ガイドによって送り出されたラベルは、台紙に載っている姿勢を保ったまま瞬時に、回転しているドラムの周面に真空吸着される。すなわちラベル片方が、空中でフリーな状態となることを最小限に抑えているわけである。
剥離後のラベルの前方部は、すぐにドラム周側面の真空吸引穴に吸い取られて保持され、ラベルの後方部は台紙上に付着している状態である。つまりラベルの前後の両端部が保持され、ラベルは安定した姿勢を保っている。そしてラベルの剥離が進行すると順次、ドラム周側面の真空吸引によって吸い取り面が拡大し、安定した姿勢のまま剥離ガイド上の台紙から離れることになる。その後、ドラムがラベルを吸着した姿勢を保ったまま回転移送し、ドラムが容器を押さえ付けながらラベルを貼り付ける。このように剥離から貼り付けまでの過程で、ラベルの姿勢を乱す不安定要因を介在させないのである。
これに対し、剥離後直にラベルを容器に貼り付ける方式では、ラベルの先端部がフリーになる不安定な状態が出現する。そのためラベルの貼り付け精度は、姿勢の乱れによって低下したり、容器の形状に左右されたりすることなる。
また連続ラベル送りによるラベル剥離であっても、間欠ラベル送りによるラベル剥離であっても、ドラムによる容器へのラベル貼り付けは等速回転運動であることから、貼り付けの高速化を図ることができる。
タックラベラーの貼付能力は間欠ラベル送り剥離式より、連続ラベル送り剥離式の方が高い。
連続送りタックラベラー(LR-**T)
連続ラベル送り方式によるタックラベラーの開発は1980年頃に始まり、次々とタックラベラーに関する特許が出願されている。連続送りロールラベラー(LR型)の1号機を出荷した同年(1982年)に、連続送りタックラベラーの1号機を音響機器メーカーに納入している。
以下に、そのタックラベラーに関する特許について概観する(以下図、写真)。
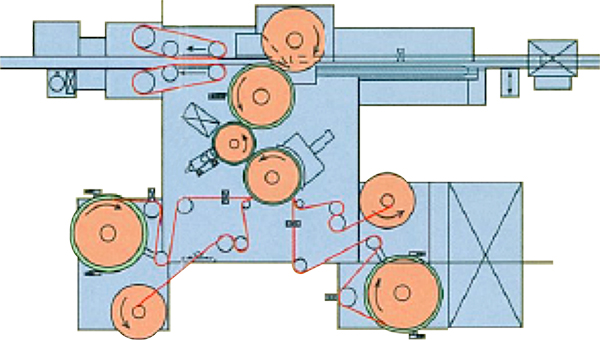
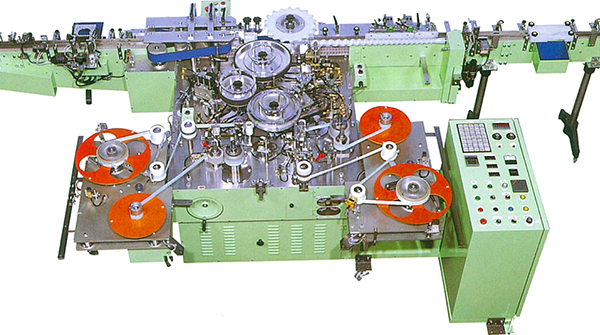
タックラベルに関する特許
最初のタックラベラーのモデルは、ラベル剥離装置と貼付ドラム、貼付スターホイールからなるものであった。連続送りによるタックラベルの供給と、ラベル位置修正機能付き貼付ドラムによって、容器の連続搬送に対応した高速で、精りによるタックラベルの供給と、ラベル位置修正機能付き貼付ドラムによって、容器の連続搬送に対応した高速で、精度の高いラベル貼り付けを行うことを可能にした(特願1981.11、以下図)。
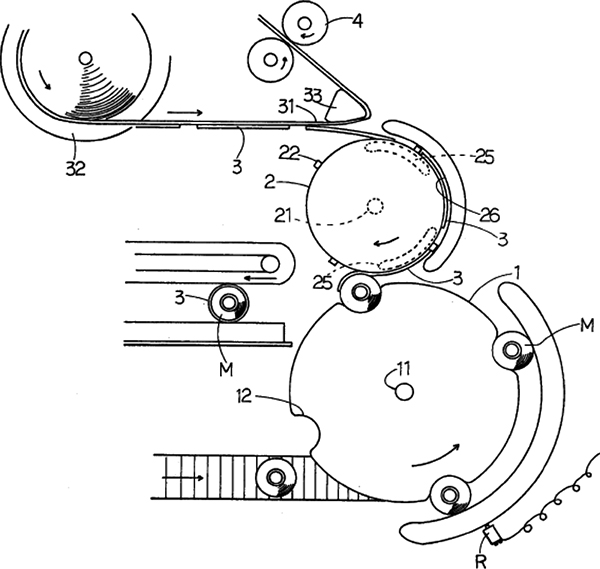
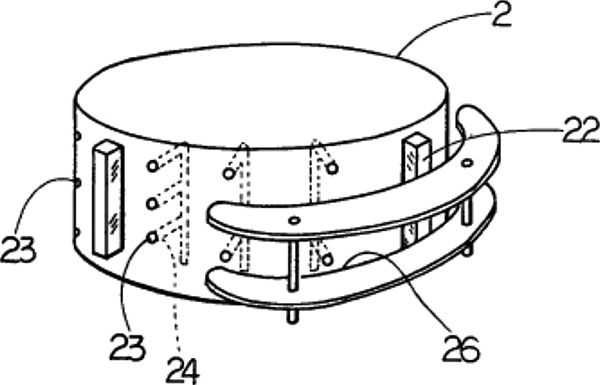
さらに、貼付ドラムの側面に加熱装置を設けてタックラベルを加熱し、接着剤を軟化活性化させるとともにタックラベル自体も軟化させる。冬季夏季を通して一定の粘着性を持たせることで、タックラベルの反り返りを防ぐことができる(特願1981.12、以下図)。
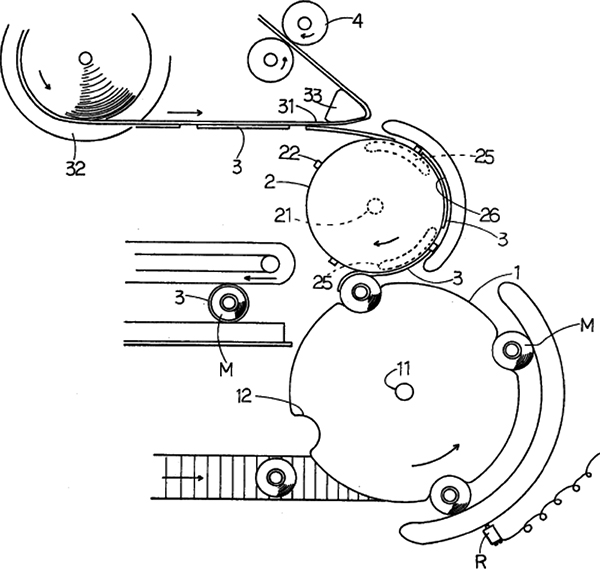
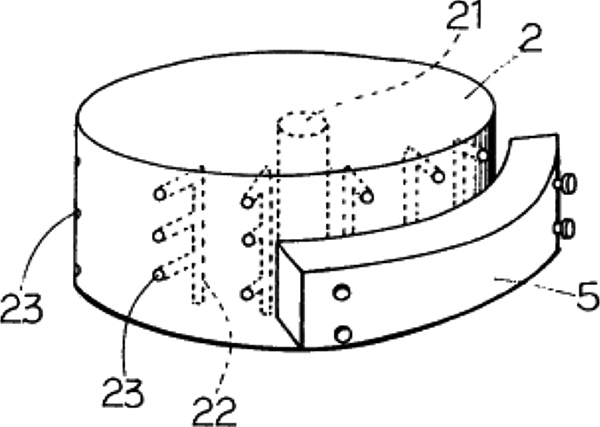
次のモデルは、ラベル剥離装置と貼付ドラムとの間に移送ドラムを設けるというものである。
タックラベルの接着面を移送ドラムに貼り付けてしまい、剥離ガイドで移送ドラムからタックラベルを剥がして貼付ドラムに受け渡す。これにより、高速でタックラベルを剥離して貼付ドラムへ受け渡し損なうことがなくなる。また剥離後の移送ドラム上のタックラベルの表に印字することで、タックラベルの管理が容易となる(特許1982.7、以下図)。
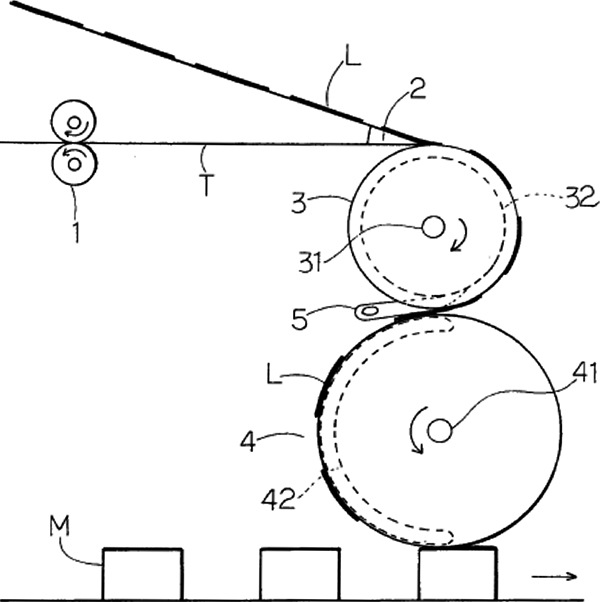
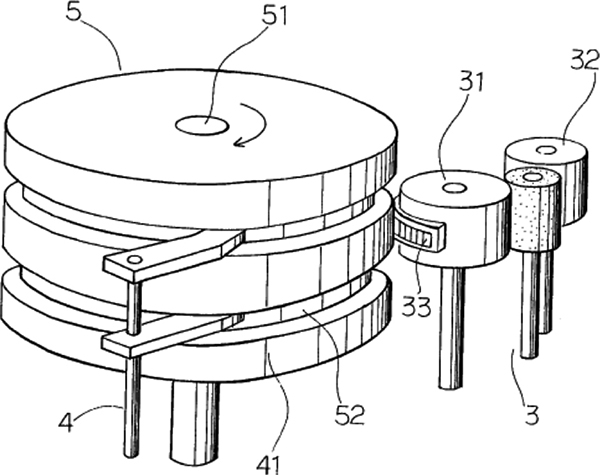
また、タックラベルのドラム移送に伴う課題も次々に解決していった。移送ガイドからラベルの接着面に向けてエアーを吹き付けることで、接着面がガイドに接触してジャミングを引き起こすことを防ぐ(特願1983.2、以下図1枚目)。
また、吸引ドラムと並行に配置した、非着処理の多数のローラー(51)で案内しつつ、タックラベルを移送する。これにより、ジャミングやラベルの折れ曲がりを防止して、タックラベルの高速移送を可能にする(特願1983.3、以下図2枚目)。
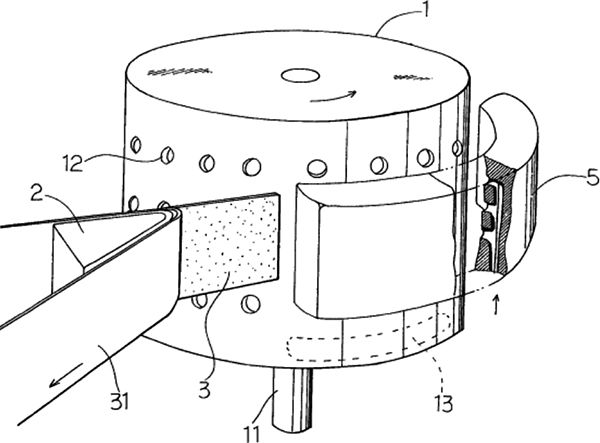
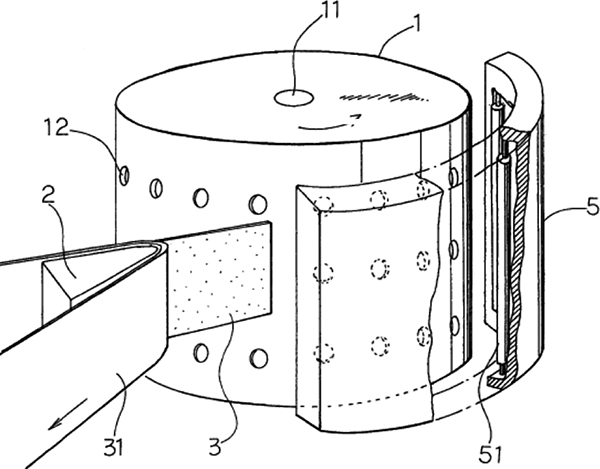
あるいは、タックラベルの修正ドラム(5)で、床面の回転ディスク(8)に付着する接着剤を自動的に除去するクリーニング装置(81)を配置した。ラベルの無駄をなくし、接着剤の除去作業が不要となる(特許1983.8、以下図1枚目)。一方、切り込み工程を組み込んだタックラベラーを提案している(特願1983.12、以下図2枚目)。

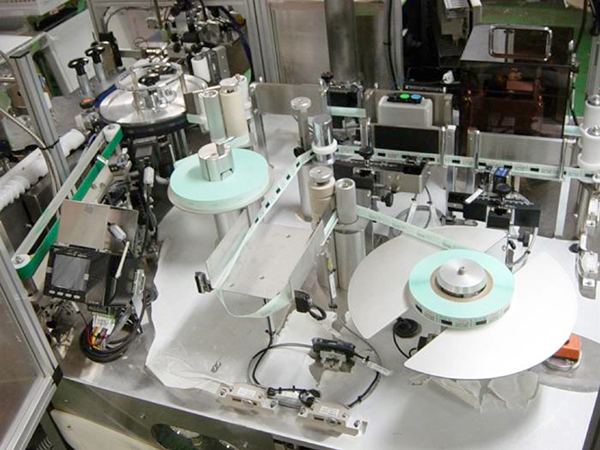
台紙上の未切断のタックラベルを剥離する直前に、カッター(3)で切り込みを入れ、容器にタックラベルを貼り付け、台紙は巻き取られて回収されるというものだ。タックラベルの製造工程から打ち抜き工程を省くことで、コスト削減を図ることができる。
以上のように、タックラベラーの分野に遅れて進出した当社は、真空吸引式ドラムや連続ラベル送り剥離方式という、他社にない方式の活用で、ラベル貼り付け精度や速度を向上させた。
さらに印字装置や印字検査、不良ラベルの除去装置などを搭載する多機能で、総合的なラベリングマシンとして発展していくことになる。また容器の形状に合わせた搬送方法や、貼り付け方法を発案している。例えば搬送やラベル貼り付けが困難である、アンプルや注射器のような対象物の供給・搬送方法、貼り付け方法を次々と確立していった。
連続送りの確立と間欠送りタックラベラーヘの移行
ロールラベラーの技術をベースとして、連続送りによるタックラベラーの高速化を進め、連続送りの完成形を確立した(2002 年の実施例)。それは、修正ドラム・印字ドラム・貼付ドラムといった吸引式移送ドラムを駆使したスタイルである(以下図、写真)。
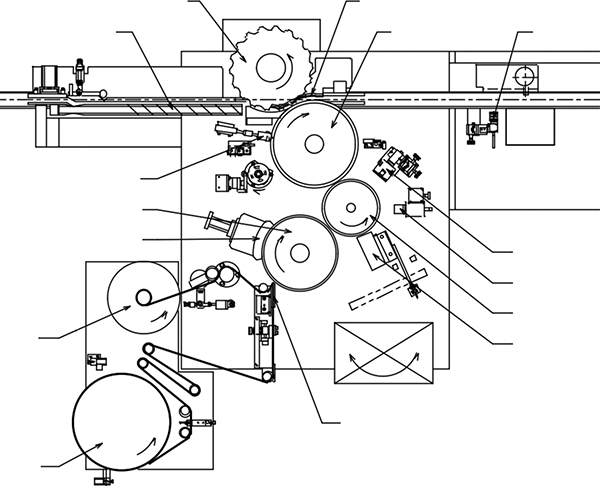
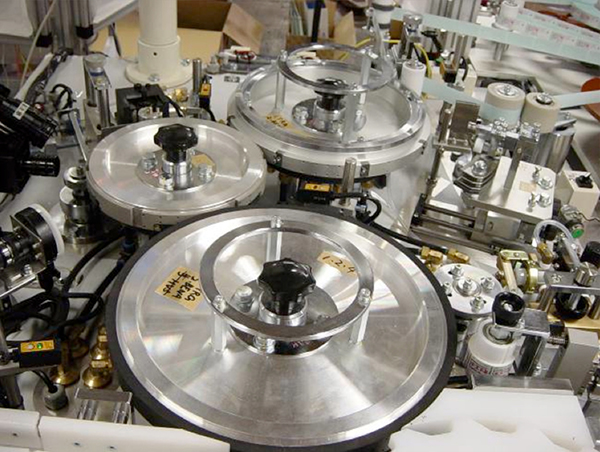
連続送りタックラベラーの高機能化
その連続送りタックラベラーには、製薬企業の高い品質要求に応える様々な機能を備えることができる。しかも、フレキシブルに顧客要求に対応できる方式である。インクジェットプリンター、レーザーマーカなどの様々な機種の印字装置を搭載することも可能だ。あるいは印字検査や不良ラベル排出、ラベル貼り付け検査などを実施・管理するという多岐にわたる機能を備えたものであった。
間欠送りタックラベラー(LK型、LKS型)への移行
サーボモーターと制御システムの発達に伴い、高い精度の間欠ラベル送りが可能となってきた。タックラベラーの小型化やコスト削減を目指して、間欠ラベル送りへの移行が進められることとなる(以下図、写真)。
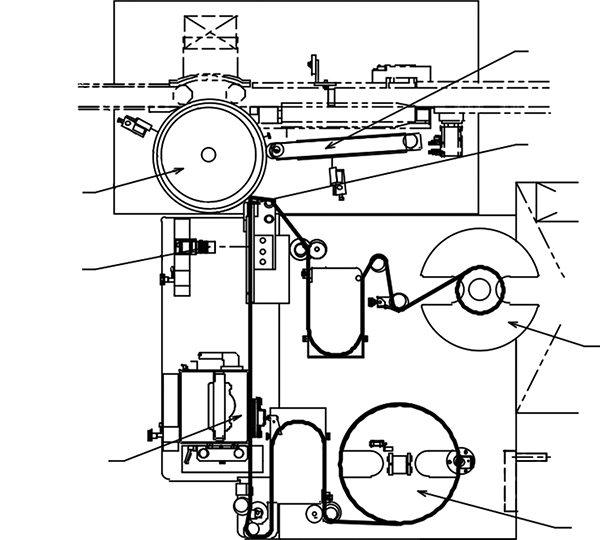
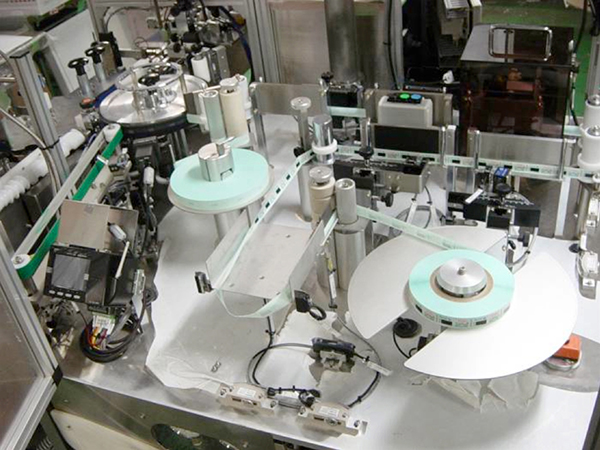
ラベル送りを連続から間欠へ変えるメリットとは、何であろうか。
連続送り方式では修正ドラムや印字ドラムが搭載され、かなりのスペースとそれに応じたコストも掛かる。これに対して間欠送り方式では、貼付ドラムの側周面の動きに同調させてラベルを剥離して送り出すことができ、貼付ドラムの指定位置に正確にタックラベルを引き渡させる。真空吸引式ドラムは貼付ドラムのみとなり、機械装置全体はコンパクトなものとなる。
また停止状態で印字可能なホットプリンターやサーマルプリンターも搭載できる。合わせて、ラベルテーブルに付随するテンションローラーに換えて、ラベルバッファー装置として補助送り装置を搭載できる。
またロールラベラーで開発された新型のラベルテーブルを搭載し、台紙巻き取りテーブルを使い勝手がよく操作性に優れたものに改良した。当社独自のラベル送り制御装置を基板から制作し、オリジナルな間欠ラベル送り制御ソフトを作成した(以下写真)。
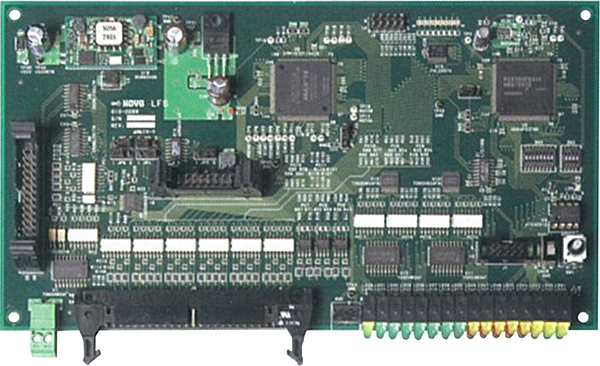
この制御装置により精度の高いラベル送り制御を実現し、ラベル貼り付け精度の向上に寄与している。こうした制御でのハードとソフトの両面でのスタンダードの確立によって、制御装置本体のコスト削減とともに、電気設計やラダー作成といった作業工程の削減にもつながった。この間欠送りタックラベラーは、機械装置と制御装置の両方について、ハードとソフトの両面からの改良が進められたものである。
一方、製薬企業から求められる品質要求はさらに高度化・厳密化しており、バリデーション(検証)が幾重にも実施され、それに対応するハードとソフトの両面での性能の向上が求められている。その実現のためには、担当営業や機械・電気設計員、機械技術員、制御技術者員の連携といった人的ネットワークの強化を図ることが重要である。
他の構成要素の進歩~特にタックラベラーとの関連
これまでは、タックラベラーの主要構成要素であるラベル送り/供給装置の発展を中心に述べた。
ラベラーの他の構成要素である貼り付け方式や、容器供給/搬送装置などについて、特にタックラベラーに関連する技術をピックアップして紹介する。もちろん、これらの技術の多くはホッパーラベラーやロールラベラーにも適用される。
貼付スターホイール
注射器やアンプル、バイアル瓶などの小型の容器では、スターホイールで回転搬送している間にラベルを貼り付ける方式が採用されている。ここでも、回転運動(公転と自転)の連鎖によるラベリング工程の構築という思想が貫かれている。その開発経過について、特許から概観してみたい。
そのモデルの原型は、タックラベラーの1号機を出荷した年の1982年の出願特許(「駆動大圧着ローラー付きスターホイール」〔1982.9、以下図1枚目〕)に示されている。貼付スターホイール(5)の内側にスターホイールと同心の圧着ローラー(6)を露出させ、貼付ドラム(1)と圧着ローラーとで容器を保持して、強制的に容器を自転させてラベルを貼り付ける。これにより、ラベルの空滑りやたわみを防止することができる。スターホイールのポケット部への接触がないこと、他のローラーで保持されていないことから、摩擦抵抗がなくスムーズなラベル貼り付けが可能となる。
また、駆動源付き圧着ローラーを小型化して、貼付スターホイールと同心でないモデルも発案している(特許1982.12、以下図2枚目)。そして、圧着ローラーを駆動させないで、貼付ドラムの回転のみでラベルを容器に巻き付けるというモデルにたどり着く(特許1983.3、以下図3枚目)。貼付スターホイール(5)の内側にフリーの圧着ローラー(6)を露出させ、貼付ドラムと圧着ローラーとで容器を保持し、自由に容器を回転させてラベルを貼り付ける。構造が簡単であり、回転速度の制御が必要なく調整が容易である。
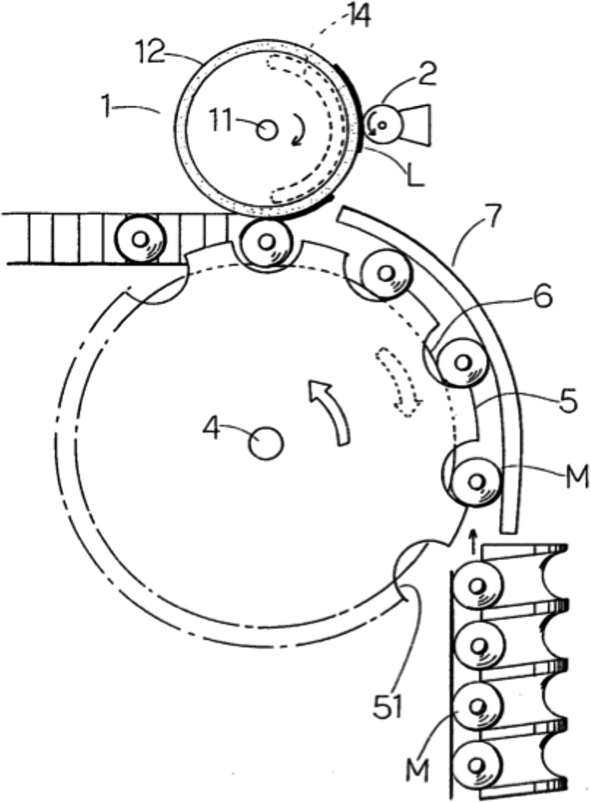
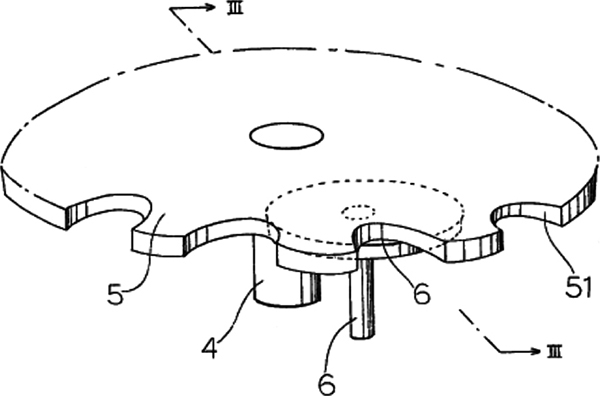
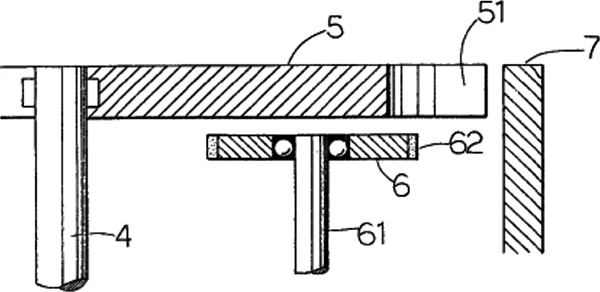
一方、「山形状周面貼付ドラム」の特許(2006.6、以下図)では、貼付スターホイールではないが、2つのフリーローラーに寝かせて搬送されている注射器などの小型容器にラベルを貼り付ける方法が記載されている。この特許の主眼は、貼付ドラムの外周面を山形状周面とすることによって、形状の誤差のある容器が混在していてもラベルをシワなくきれいに貼り付けることができるというものである。
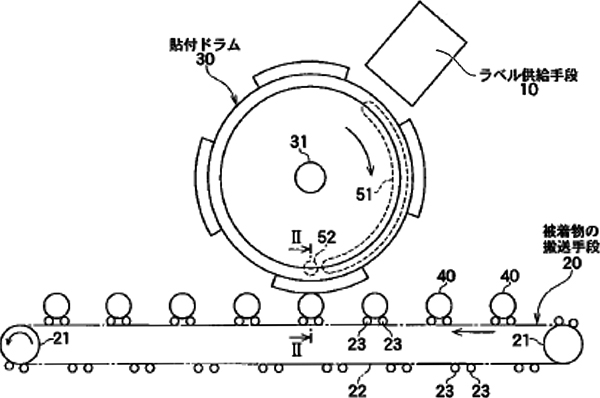
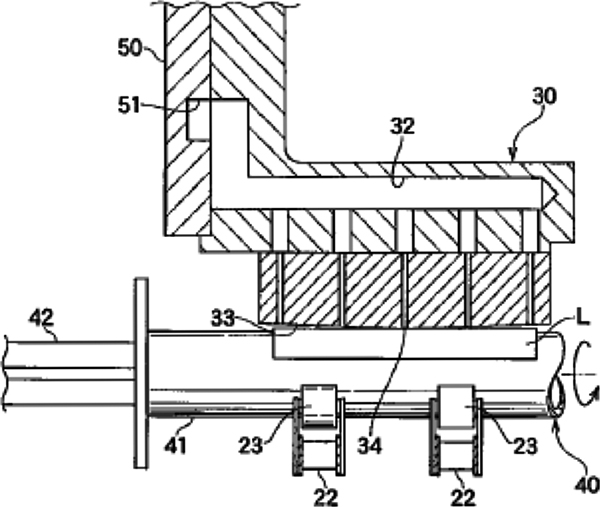
伸縮ローラー付き貼付スターホイール
このような経過を辿り、スターホイールによるラベル貼り付け方式は特許「伸縮ローラー付き貼付スターホイール」(2009.3、以下図)でその完成形を確立した。
貼付スターホイールに一対の伸縮可能な容器保持ローラーを複数備え、貼り付け時に容器を貼付ドラムとの3箇所で線接触して保持する。ローラーの伸縮により、容器が貼付ドラムに連続して圧着されてラベルの貼り付けと仕上げを同時に行うものだ。3箇所の線接触によって容器が高速で回転しても良好な鉛直性を保つことができ、ラベル貼り付けを正確に行うことができる。この貼り付け方式は、ドラムとR仕上板による方式と同じ考え方に基づいている。すなわち貼付ドラムの回転に伴って容器が自転しながら公転して、ラベルを貼り付けて巻き付け仕上げるというものである。
ターレットロータリーによるラベル貼りつけ方式にも、同様な考えに基づく様々の機構が考案されている。当初この方式は、「ロールラベラーの開発とその発展」でも述べたように、ロールラベラーでドリンク剤などの小型容器への高速ラベル貼り付け方式として開発された方式であった。バイアル瓶などの一層小型な容器に、精度よく比較的速い速度でラベルを貼り付けるために、タックラベラー(LKS型)に採用されたのである(以下写真)。
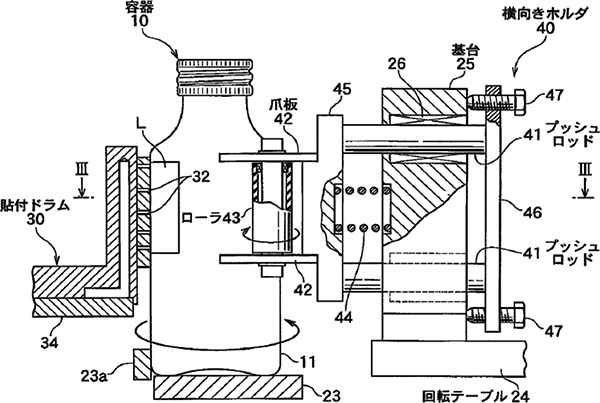
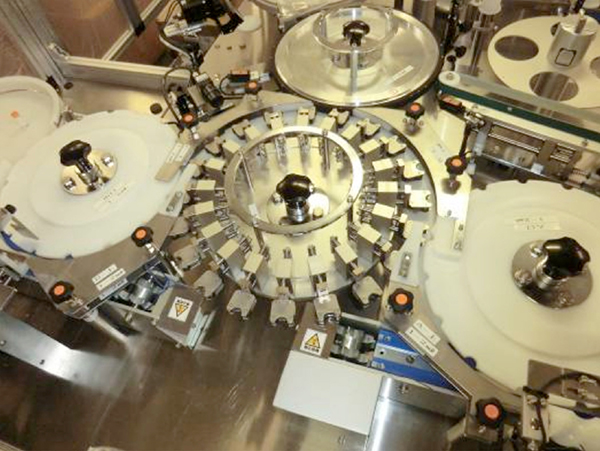
不安定容器の供給装置
アンプルやバイアル瓶(注射薬液充填)など不安定な容器は、供給・搬送している間に倒れることが頻発し、そのたびに機械装置の運転を停止し、倒れた容器を起こさなければならなかった。このため生産効率が低下し、容器の転倒を防ぐ供給・搬送方法が求められていた。
還流ガイド付き容器供給コンベアと供給スターホイール(特許1986.9)
容器を供給するベルトコンベアとその下流側にスターホイールを配置した容器供給装置では、供給面積を徐々に狭める「絞り込み路」と供給面積を徐々に広める「開放路」とを設けた還流ガイドを設けている(以下図)。
これにより、容器の転倒や詰まりを防止し、スムーズな容器供給を行うことができる。
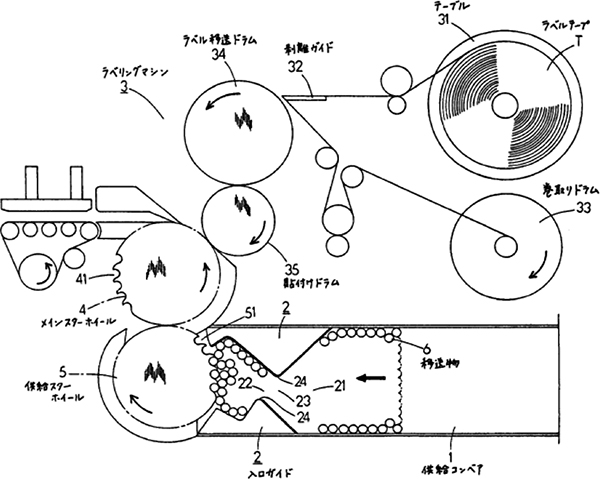
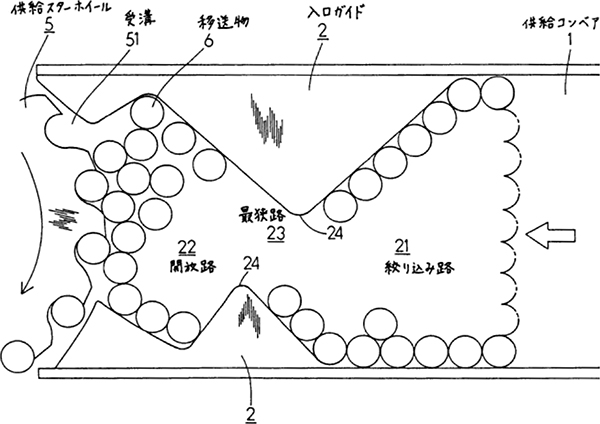
不安定容器の供給装置、傾斜供給コンベアと供給スターホイール(特許2009.1)
容器を供給するベルトコンベアとその下流側にスターホイールを配置した容器供給装置では、ベルトコンベアの搬送面をスターホイールに向けて下り勾配に傾斜させ、不安定容器をスターホイールに向けて前傾姿勢で搬送するようにする(以下図)。これにより、不安定容器の転倒を防止して搬送することができる。容器供給コンベアに独特な形状の還流ガイドを設け、コンベア後方部へ還流する容器の転倒を防止する。これは実地に、コンベアで搬送される様子を観察することによって、容器の詰まりや転倒を防ぐ方法を実現させたものである。アンプルの集合体が流体のごとく動く様を観察しながら、その流動の特性を理解して発想した形状である。
また、供給コンベアを搬送方向に傾けるというアイデアは、重心が高く倒れ易いアンプルをいっそのこと初めから一方向に倒してしまえば、倒れようがないという「逆転の発想」から生み出されたものである。搬送方向のスターホイールにもたれかかったアンプルは、倒れようにも倒れられないわけである。この2つの要素の作用で容器供給が格段にスムーズに行われるようになり、不安定容器のラベル貼り付けの効率化が図られた。
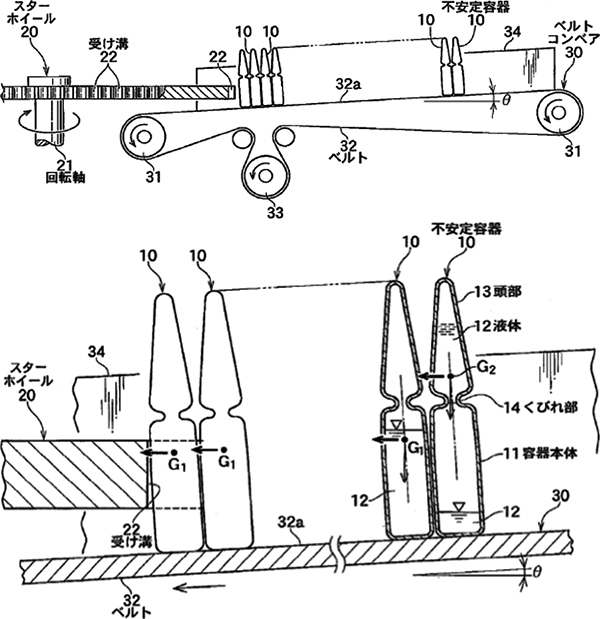
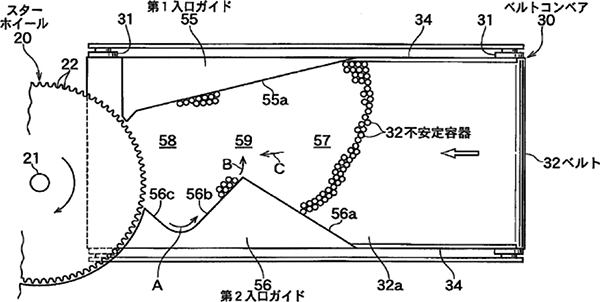
直立困難な搬送体の搬送
注射器などの直立困難な容器を搬送する方法として、幾つかの搬送手段が採用され実機に活用されている。
その1つは鉛直に立てた両側のコンベアに、搬送体の張出部を引っ掛け吊り下げて鉛直状態のまま直線搬送するという方式である(特願1998.10、以下図、写真)。
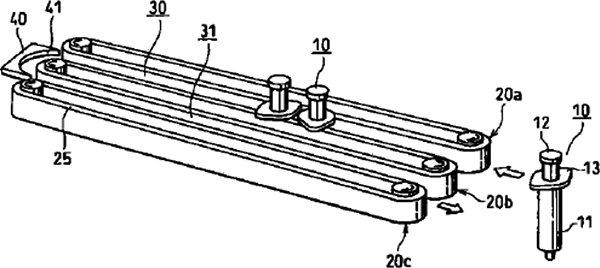
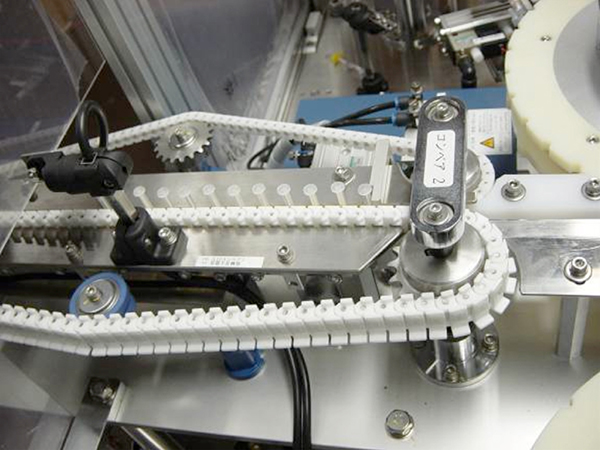
シュリンクタックラベラーには、注射器に貼り付けられたシュリンクタックラベルを、この搬送状態で熱風を吹き付けて収縮させる場合もある。あるいは、スターホイールのポケット部に搬送体の張出部を引っ掛け、吊り下げて回転搬送する方式も併用されている(以下写真1枚目)。
もう1つは、先に述べたように注射器を2本のフリーローラー上に寝かせて搬送し、その姿勢のままラベルを貼り付けるというものである(以下写真2枚目)。ローラー上の注射器は、縦型タックラベラーの貼付ドラムに接して圧着され、貼付ドラムの回転に伴って自転しながらラベルが貼り付けられる。
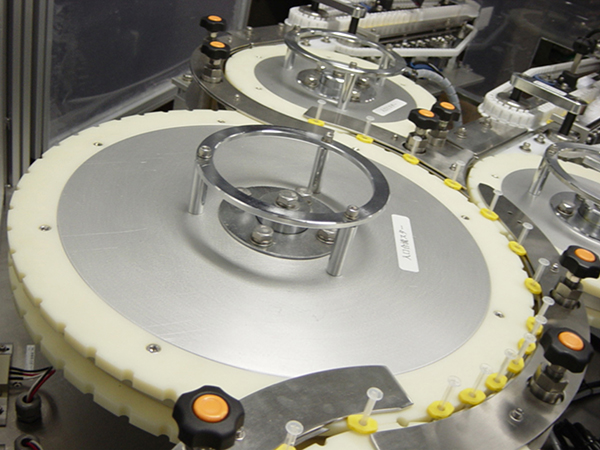

ラベル供給部の昇降装置(特許1995.3)
ラベルの貼り付け高さを変更するために、供給部上盤を支えるスクリュー軸の回転によって供給部の上盤を昇降することができる(以下図)。これにより品種切り替えに際しラベルの貼り高さの変更が容易になる。
多品種へ兼用する機械への要求が強まる中で、この機構は多くの機種(タックラベラー、ホッパーラベラー、ロールラベラー)に採用され、年々出荷に占める割合が増加している。特に近年のタックラベラーのLKS型やLK型にはほとんどこの機構が搭載されている。
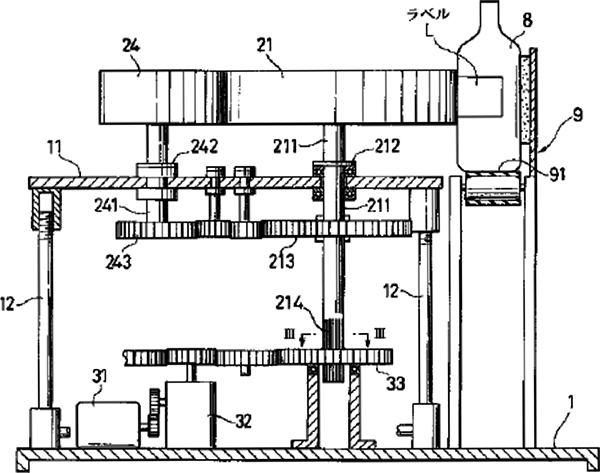
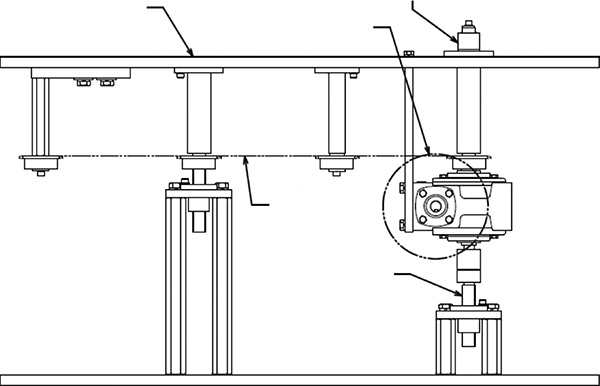
容器の方向規制装置
取手付き容器や不定形容器の向きを一定方向に揃えて、ラベルの貼り付け位置を限定するために開発された装置である。その概要を紹介する。
取手付き容器のスタ一部カムアーム式方向規制装置(特願1983.9)
スターホイールのポケット部で取手付き容器を自転させながら搬送し、容器の回転を規制する修正アームがポケット部に突き出て容器の自転を停止させる(以下図1枚目)。
これにより、取手付き容器の一定位置にラベル貼り付けを行うことができる。従来の光電管を使用する複雑の装置が不要となる。
取手付き容器の方向規制ターレット(特許1993.7)
ターレットロータリーでは、ベースカップ上の取手付き容器をベルト駆動により自転させつつ、方向規制板の突き出しによって容器の自転を停止させ、容器の取手の向きを揃えて貼付ドラムによるラベル貼り付けを行う(以下図2枚目)。
ターレットロータリー式の取手付き容器の方向規制は、この方式で実施されている。
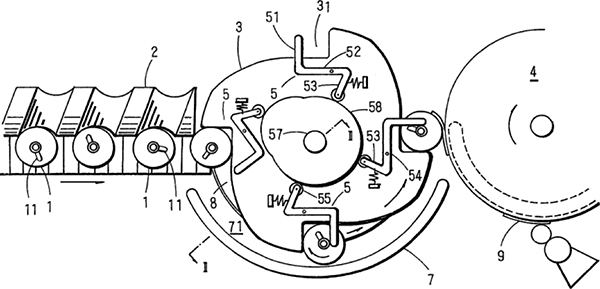
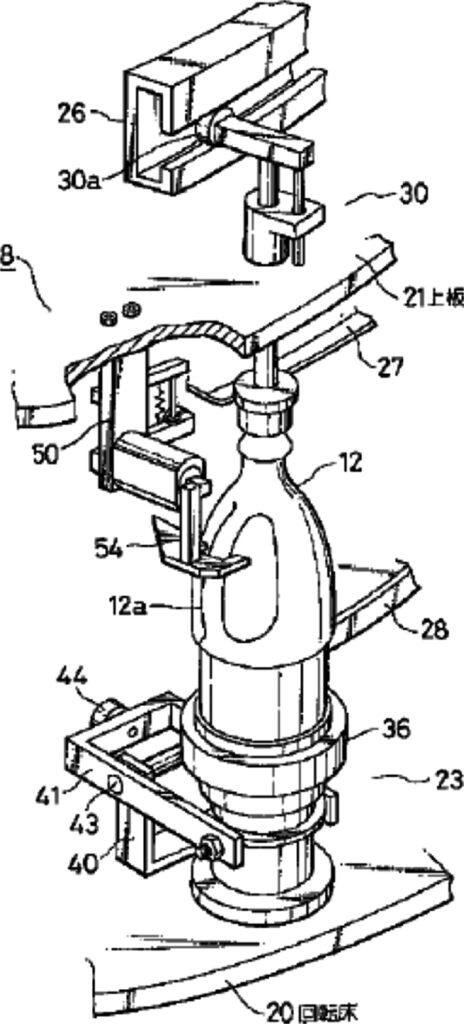
窪み付き軽量容器の方向規制装置(特願2001.5)
小型軽量で不安定な窪みをもつ容器を、スターホイールで搬送しながら隣接する修正ベルトによって強制的に回転させ、定位置の容器窪み部を負圧吸引部で吸着し、次工程に受け渡す(以下図)。
これにより、これまで対応が困難とされてきた小型軽量で不安定な窪みを有する容器を、確実に方向規制することができる。
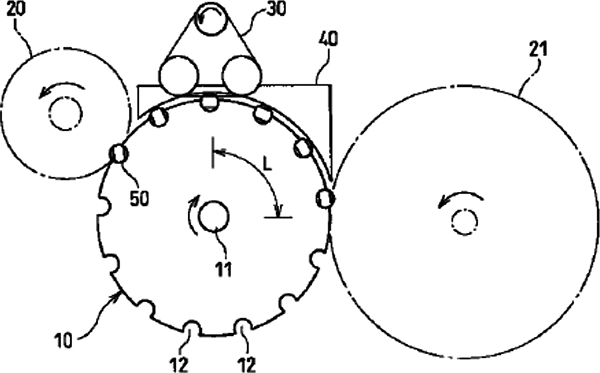
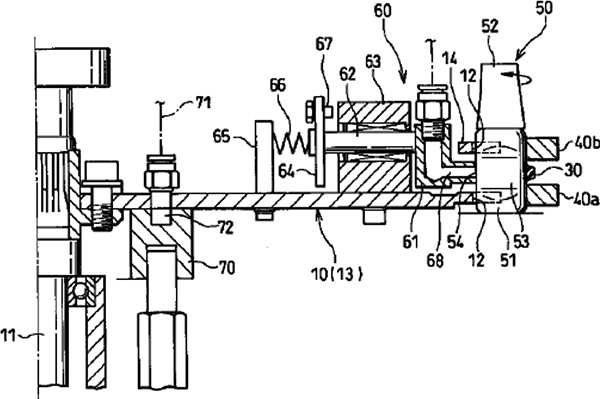
コンベアラインでの取手付き容器の方向規制(実施例)
取手付き容器を反転ベルトで強制的に自転させ、方向規制アームの突き出しで停止させ、容器の取手位置を一定方向にそろえる(以下図)。
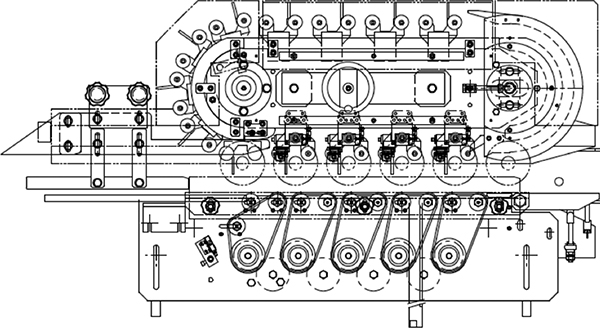
不良ラベル除去装置
容器にラベルを貼り付ける前に、不良ラベル(印字不良や継目付きラベルなど)を除去することで、不良ラベルを貼り付けた容器を後の工程で排出する必要がなくなる。これにより、不良ラベル容器の排出や容器からのラベル剥がしといった作業工程が省かれる。
この装置は、当初ロールラベラーの不良ラベルの排出に適用された方式であるが、この考え方はタックラベラーにも適用され、ラベルの管理を正確に行うことができることとなる。印字不良や異種ラベルが容器に直接貼り付けられずに、排出された数量を正確に把握することができる。
医薬品などに要求される高い品質基準に対応するには不可欠な装置として、日本内外のタックラベラーの標準装置として一般化することになる。
クシ式不良ラベル除去装置(特許1988.11)
貼付ドラムでラベルを搬送中に不良ラベル(継目や印字不良など)検知信号によって、ラベル除去クシが貼付ドラムの溝に出入りして不良ラベルを除去する(以下図1枚目)。
これにより、容器にラベルを張り付ける前に不良ラベルを除去することができ、最終製品の検査はラベル有無だけとなる。
台紙巻き取り式不良ラベル除去装置(特願2005.12)
貼付ドラムでラベルを搬送中に不良ラベル(継目や印字不良など)検知信号によって、台紙テープが貼付ドラムに突き出して、糊付けされラベルに接触させて不良ラベルを除去する(以下図2枚目)。
除去された不良ラベルは巻き取られて保管されるとともに、不良ラベルの記録と管理が正確に行うことができる。
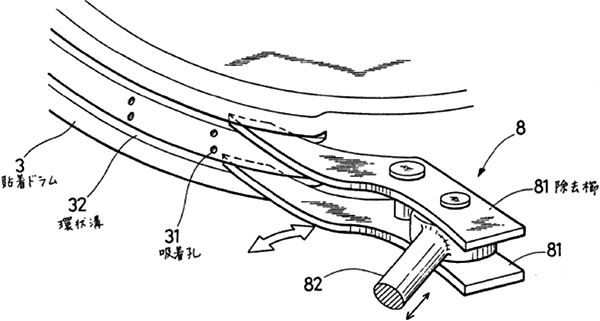
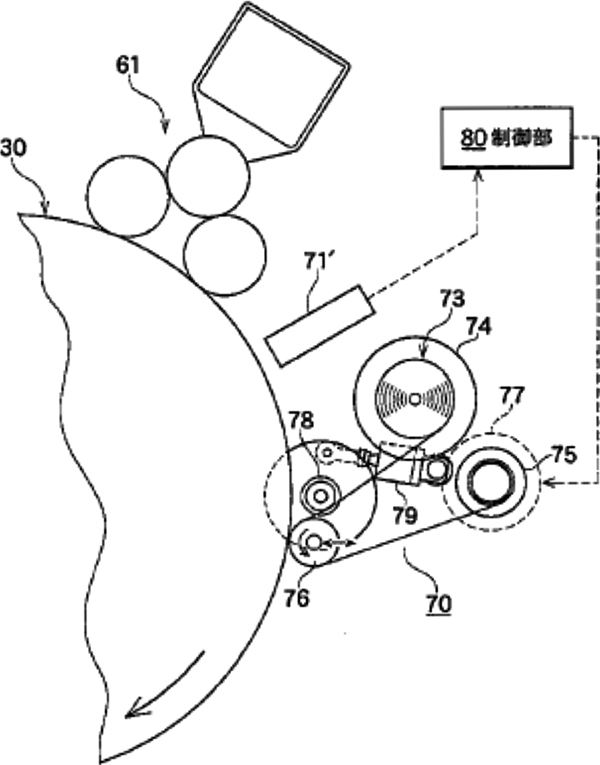
ローラー付きクシ式不良ラベル排出装置(特願2007.7)
不良ラベルを検知するセンサーからの信号によって、ラベル除去クシ(内側と外側)が貼付ドラムの溝に出入りして不良ラベルを除去し、剥離した不良ラベルを一対の排出ローラーの回転によって強制的に排出する(以下図1枚目)。長いラベルの排出に対応している。
タックラベルのベルト式不良ラベル排出装置(現行タックラベラーに装備)
タックラベルの接着面に不良ラベル除去ベルトを突き出して、巻き取って排出する(以下図2枚目)。現行のタックラベラーの標準タイプとして使用されている。
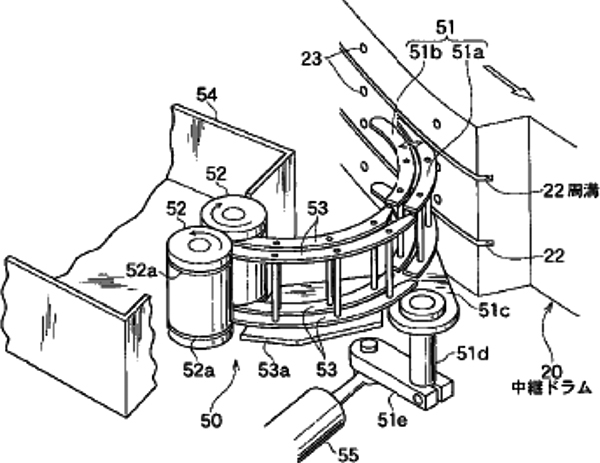
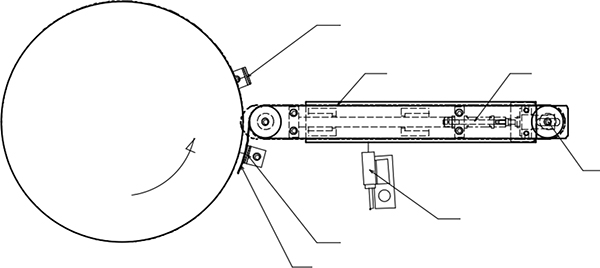