This Company has for the last 44 years since 1968 brought over 3200 products into the world. I have thought it best to clarify “what the technical background for the acceptance of the labeling machine not only in Japan but throughout the world” and “what the idea behind the emergence of this technology” were by tracing the history focusing mainly on the patents applied for. Mr. Kyoichi Yamashita, the Chairman of the Company, is the founder and as well as the inventor and also the developer of the labeling machine. He made almost all of the inventions and actually engaged in the fabrication of the machines and in the filing of patent applications. The details I am about to state here are to a large extent reflective of the situation as it was at the time of development and as related by Mr. Yamashita and owing to his utterances about the ideation process. It is needless to say that the “Details of the Invention (Technical Grounds),” the “Purpose of the Invention,” and the “Effect of the Invention” started in the patents are the result of Chairman Yamashita’s thoughts. The number of patents applied for in Japan amounts to 258 and in countries abroad to 63, with the total number of patent applications being 321. Systematically assessing the Details and Purposes of the inventions we have shown a chronological record combining the “history of KOYO Automatic Machine Co., Ltd. as seen through its patents” and the “salient events” since the foundation of the company.We have also summed up, based on the “Machine Shipment List,” the changes over time of the number of labeling machines shipped by machine type and of the number of labeling machines shipped by customer and by field (food products, pharmaceuticalBased on these materials, we have made a summary in the form of the “Genealogy of KOYO Technology and the Development of Packaging Machines” (October 2009). Based thereon, I would like to talk about the pedigree of our labeling machines through the efforts KOYO has made. First of all, I would like to raise the question as to what the labeling machine really is. So let me given some simple explanations. products and etc.). We have also attempted to make it possible to clearly understand the positioning of our company’s technology by making reference to the “salient events” related to our labeling machines both at home and abroad and by gleaning the information from the Historical Overview of Related Companies in their respective homepages.
Labelers for production lines
Labeling machines are used, as the name suggests, to apply labels to containers or boxes. Labels are applied to a wide range of products including foods, beverages and pharmaceutical products. Labeling machines described in this document (hereafter, labeler) comprise of a part of large-scale production facilities such as sterilization units or filling machines for containers, container inspection machines, or cappers that are installed in the production line in plants.Labeling machines do not include hand labelers or simpler labelers used in retail stores or at store counters. Taking a large-scale beverage production line as an example, labels will be applied to containers filled with beverages, capped and inspected and then they will be fed to the next phase such as packaging. It is not rare that daily yield reaches several 100,000 units.
Roles of labels
Needless to say, labels give the first impression (image) of items to the consumers and, accordingly, have a great influence on their sale. They also supply customers with important information on product quality, production date (year, month, and day), raw material names, and components necessary for the customers to select products. For pharmaceutical products in particular, labels have an extremely important role to indicate names and components of chemicals that are critically related to human lives. Final products must have gone through a variety of inspections including those for mix of different labels or for printing on labels.
Classification of labelers
Labelers can be classified into several types according their applications, required capabilities or application methods. The next section explains the classification of labelers.
Classification according to the types of labels supplied
Labelers can be classified into the three types shown below according to the types of labels supplied. The 1st type is a foliage (cut label) labeler (hopper labeler). A large amount of labels precut to a specified shape are housed in a label hopper (also called as a label magazine), from which labels are taken out, fed and pasted onto containers (Photos below).
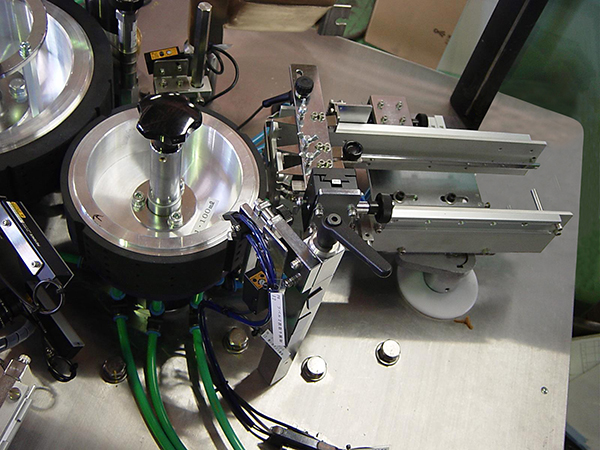
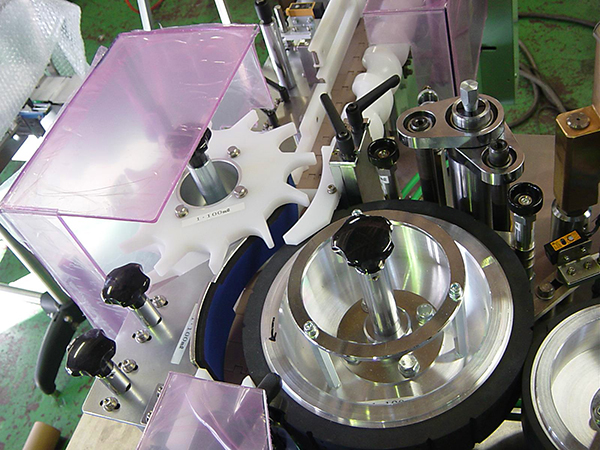
The 2nd type is a roll labeler (including whole round labelers and shrink labelers). Tape-formed labels wrapped around a paper tube into a roll at a specified diameter will be cut into predefined length, fed and placed on containers. This means that two processes that are not necessary for foliage labeler have been added, a process to take out tape labels and a process to cut those labels (Photos below).
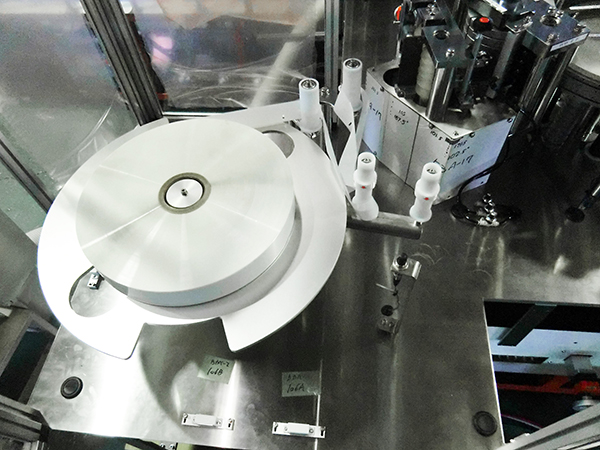
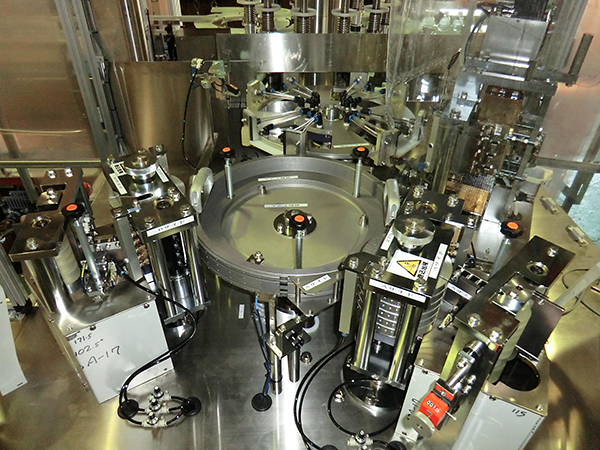
The 3rd type is a tack labeler (including shrink tack labelers) (Photos below). A tack label means precut label seal pasted on a tape-shaped mount. Label seals will be peeled off from the roll tack label of a specified diameter tape formed tack labels, fed and then placed on containers. This type feeds labels by making foliage labels (cut labels) to be tape-form labels, which is a cross system between the foliage labeler and the roll labeler. It has a characteristics to be equipped with a process to send out a roll tack labels and another process to peel labels off.
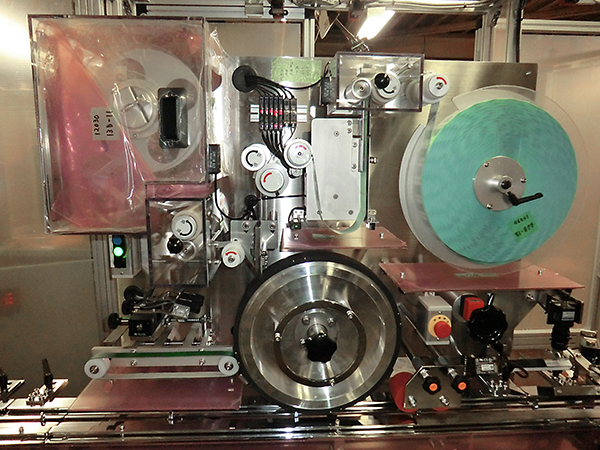
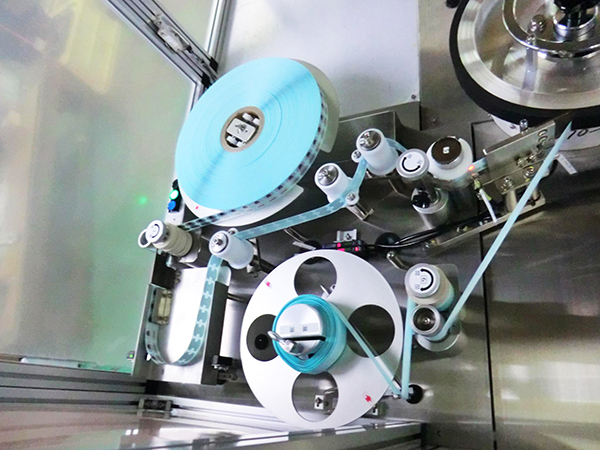
Classification according to the types of label application (fixation) systems
Labelers can be grouped into roughly two types: those paste labels directly to containers and those put labels on containers and then apply them to close-contact.
ⒶType to directly paste labels to containers with adhesives
This type can be grouped into two types. One type applies adhesive to the back surface of labels and paste to containers. The adhesives employed include: Cold glue (cement) to be applied at a room temperature; hot melt by which solid adhesive will be heated to liquefy and apply; and UV curing adhesive which is a liquid adhesive and will solidify upon exposure to a UV light after application. The other type pastes labels to a container by activating heat activated adhesive or water activated adhesive applied to the back of a label. Labels on which heat activated adhesive has been applied are called heat sensitive labels, which will be heated with a heating device (hot wind unit or an IR irradiation unit) to activate immediately before being pasted to the container.
ⒷMethod to put a label on a container and then fit close to the shape of the container
Typical example of this method is a label fit closely to the shape of a beverage PET bottle. This type does not necessarily use adhesives to apply a label to a container.
This method can also be grouped into two types. One type is a shrink labeler. In this type of labeler, a label preformed into a tube is applied over a container and allow to go through a heating unit (steam tunnel or heat tunnel) to shrink the label so that it fits closely to the shape of the container. A new type of shrink labeler has recently been commercialized, which labeler has a function to form a tape label into a sleeve. A shrink tack labeler has also been developed, which wraps a shrink tack label around a container whose head is held in position with a bobbin and heats the label to shrink to the shape (1st photo below).
The other type is a stretch labeler. While it is the same as the shrink labeler in the point it uses a preformed sleeve label, stretch labels are stretchable and they are physically stretched with a stretching unit, put over the container, and then the stretch unit is pulled out allowing the label to shrink, fit and applied to the container. A label material of a high stretch property has been developed in recent years and employed for containers with greater protrusions and indentions (Krones AG, Germany. 2nd photo below).
As we have seen so far, many labeler models with a wide range of types are currently available in the markets. In the actual industry fields, labelers are selected based on the characteristics of containers, label designs, specific advantages of different models, or cost performance. For example, foliage labelers are used for high-mix low-volume production, roll labelers for low-mix high-volume production and tack labelers for high-functionality medium-volume production.
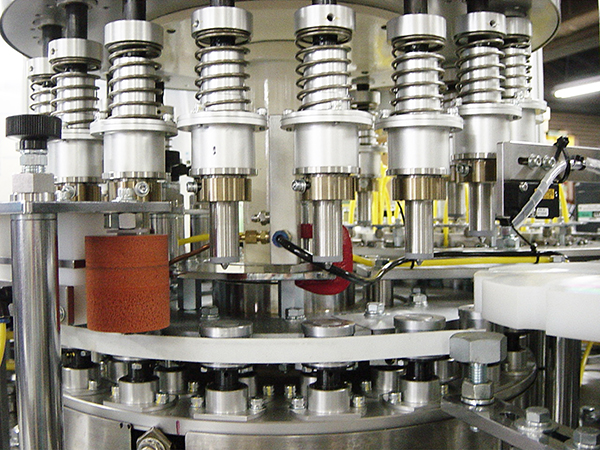
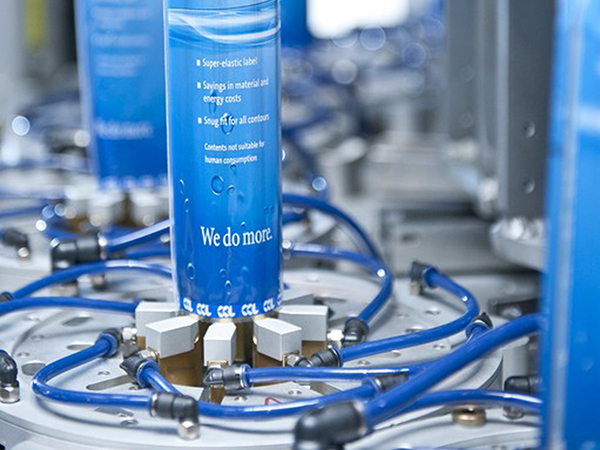