라벨 이송의 고속화를 추진하던 중에 고속 이송과 정지를 반복하여 라벨을 절단하는(간헐 라벨 이송 구조) 방식을 버리고, 차라리 연속 라벨 이송 중에 라벨을 절단하면 비약적인 고속화를 이룰 수 있을 것이라고 생각한 것 같다.
간헐 라벨 이송 구조의 최종판이 완성된 이듬해(1980)에는 연속 이송이 가능한 로터리 커터의 특허 및 구조의 특허가 잇달아 출원됐다. 이는 완전히 새롭게 개발된 완성품들이 판매되었음에도 불구하고, 시장 수요를 선점하고 더 높은 곳으로 가기 위해 또 다시 새로운 제품 개발에 매진했다.
- 목차
- 연속 라벨 이송 대응의 라벨 절단 구조
-
연속 라벨 이송 구조
- 압착 롤러 전환식(특허 1980.2, 특허 1980.4)
- 양쪽 이송 드럼 상대식(특허 1980.5.16, 특허 1980.5.30, 미국, 대만, 한국 특허 1981)
- 가변 직경 드럼 구동 부가식(특허 출원 1980.6.5, 특허 1980.6.23, 특허 1980.7.2, 특허 1980.7.14, 특허 1980.7.25, 특허 1980.8, 미국·대만 특허 1981, 미국·대만·한국 특허 1981, 특허 1981.6 등)
- 변속 구동 기어 전환식(특허 1981.10, 특허 1981.11, 특허 출원 1982.3, 특허 출원 1982.3, 특허 출원 1983.2, 특허 출원 1983.7[최종형], 미국·대만 특허 1985)
- 라벨 공급 자동 교환 방식의 고안
- 라벨 펀칭 유닛의 도입
- 롤 라벨 자동 공급 장치 개발
- 고속 부착 방식
연속 라벨 이송 대응의 라벨 절단 구조
연속 라벨 이송에 대응한 로터리 커터로써 서로 마주 보는 2개의 회전 칼날(1, 2)이 연속 회전하는 ‘가이드 클로(16)를 장착한 양쪽 회전 칼날식 로터리 커터’를 개발하고 특허(1980.4)를 취득했다.
고정 칼날·회전 칼날식 로터리 커터의 약점이었던 고정 칼날 조정이 번거로웠던 점과 라벨 이송을 일시 정지시켜야 했던 점을 극복하기 위해 개발된 것이었다(아래 그림).
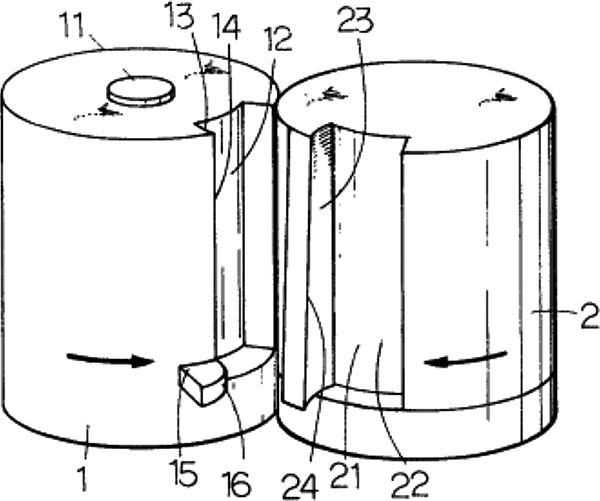
연속 라벨 이송 구조
이 시기에 연속 라벨 이송에 대응한 로터리 커터의 개발과 동시에 라벨 이송 구조의 개발이 줄을 이었다. 1980~1983년이라는 겨우 4년 동안 연속 라벨 이송 구조에 관한 특허 출원은 무려 20건 이상에 달한다.
압착 롤러 전환식(특허 1980.2, 특허 1980.4)
원둘레가 약간 다른 고속 구동 드럼(2)과 저속 구동 드럼(3)을 갖추고, 라벨 속도를 검지하는 광전관(R1, R2)의 신호에 따라 고속 측과 저속 측의 압착 롤러(4, 5)를 전환하여 라벨 이송 속도를 제어하는 것이다. 이송 드럼에 칼집을 내 그 간격을 조정함으로써 이송 속도를 조정한다(아래 그림 1장째).
양쪽 이송 드럼 상대식(특허 1980.5.16, 특허 1980.5.30, 미국, 대만, 한국 특허 1981)
둘레가 긴 이송 드럼(3)에는 전자 클러치를 통해, 둘레가 짧은 드럼에는 일방향 클러치를 통해 구동 전달하고 있다. 전자 클러치의 전환으로 둘레가 긴 이송과 둘레가 짧은 이송을 반복하여 라벨 이송을 제어한 것이다(아래 그림 2장째).

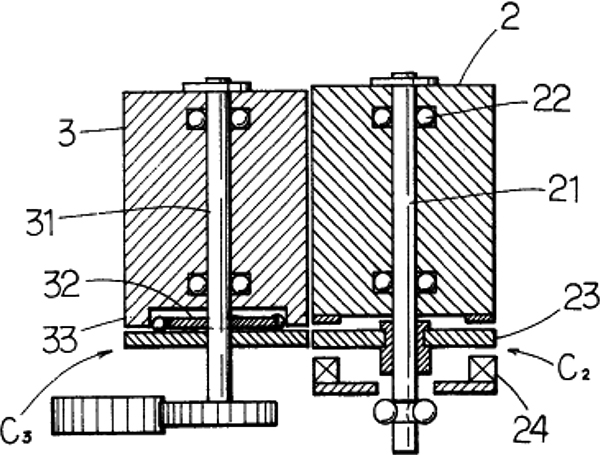
가변 직경 드럼 구동 부가식(특허 출원 1980.6.5, 특허 1980.6.23, 특허 1980.7.2, 특허 1980.7.14, 특허 1980.7.25, 특허 1980.8, 미국·대만 특허 1981, 미국·대만·한국 특허 1981, 특허 1981.6 등)
둘레가 긴 드럼과 둘레가 짧은 드럼의 전환에 의한 라벨 이송 제어와 함께, 같은 신호로 전환하는 가변 직경 드럼의 구동 전달을 통해 가변 직경 드럼의 직경이 증감하면서 미소한 회전 구동의 대소를 제어하는 것이다. 이에 따라 정밀도가 높은 라벨 이송 구조를 확립했다(아래 그림).
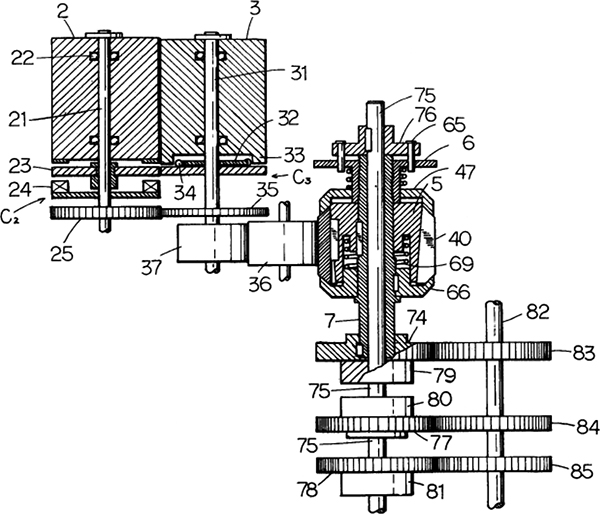
변속 구동 기어 전환식(특허 1981.10, 특허 1981.11, 특허 출원 1982.3, 특허 출원 1982.3, 특허 출원 1983.2, 특허 출원 1983.7[최종형], 미국·대만 특허 1985)
라벨 이송 드럼(1)에 압착 롤러(11)를 압착시켜 감속 기어(21)와 증속 기어(22)의 전자 클러치(C1, C2)의 전환으로 대이송과 소이송을 반복하여 라벨 이송을 제어한다. 라벨 테이프를 인쇄에 맞춰 일정한 속도로 이송하는 것이다. 품종 전환에 따라 라벨 길이가 달라지면서 형을 교환해야 할 때는 해당 품종의 이송 드럼과 교환한다(아래 사진, 그림).
위와 같이 연속 라벨 이송 구조의 변천을 살펴보면 정밀도가 더 높은 라벨 이송을 실현하기 위해 다양한 고안과 구현을 거듭하면서 미소한 라벨 이송의 증감을 제어하는 구조를 확립한 것을 알 수 있다. 이 연속 라벨 이송 장치는 더욱 단순한 방식을 통해 연속적으로 테이프형 라벨을 공급하는 기계적인 난제를 해결했다. 고정 칼날·회전 칼날 로터리 커터와 함께 오랫동안 롤 라벨러에 탑재됐다.
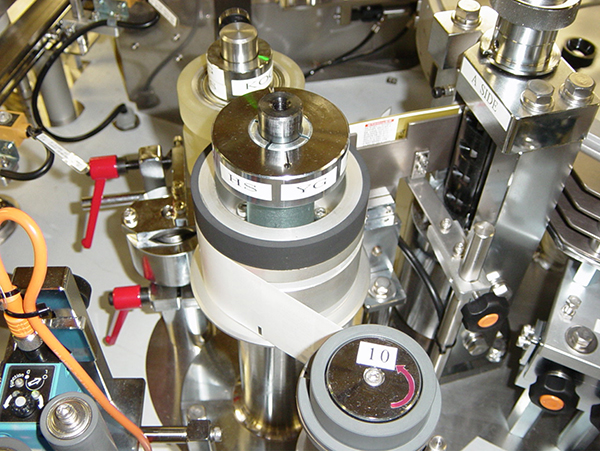
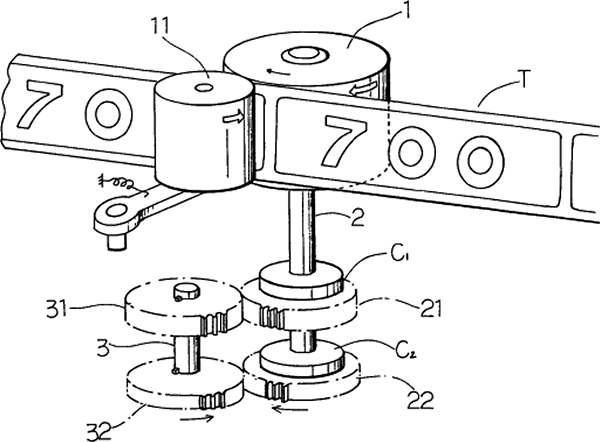
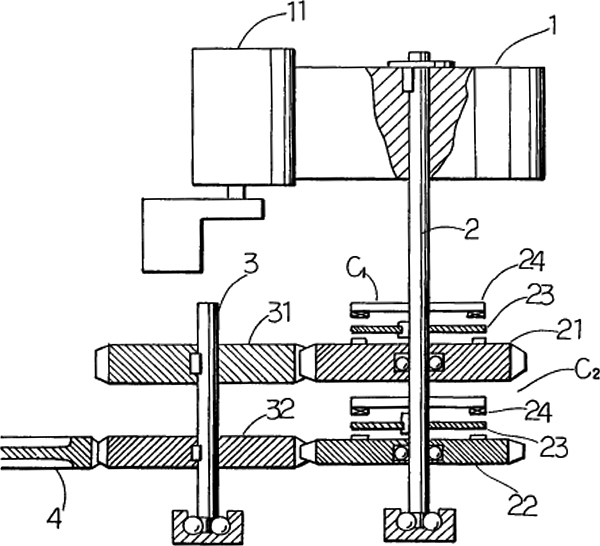
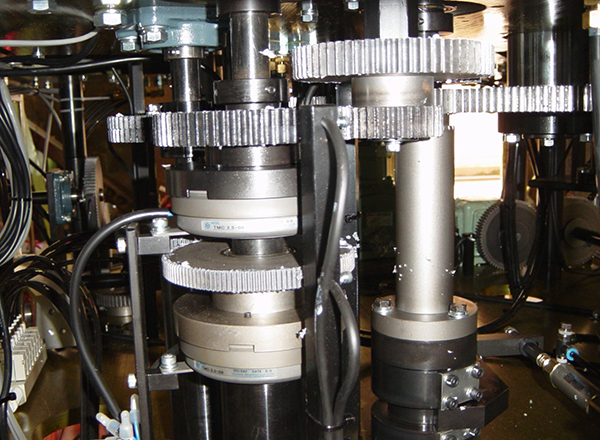
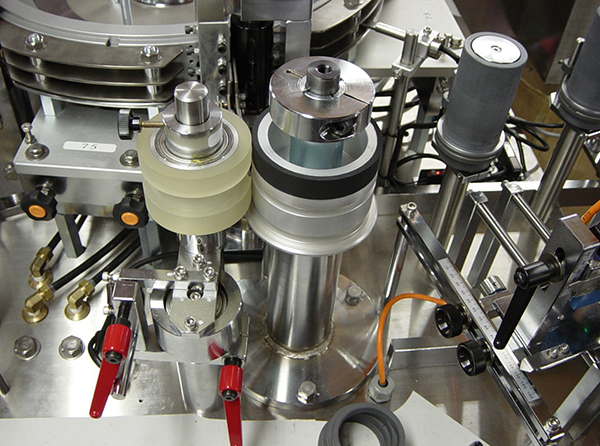
라벨 공급 자동 교환 방식의 고안
잇달아 고안된 연속 라벨 이송 구조의 구체화와 함께 연속 운전을 시키기 위한 라벨 공급 자동 교환 방식도 잇달아 고안됐다(1980년 6월~1984년 6월).
이는 롤 라벨을 보충하고 정렬하기 위해 기계 장치의 운전을 정지시킬 필요가 없는 것이다. 롤 라벨러에 라벨 공급 장치를 2유닛 탑재하여, 한쪽 유닛의 라벨 공급이 끝나면 다른 쪽의 유닛에서 자동으로 라벨이 공급됨으로써 끊임없이 라벨링이 이루어지는 것이다(아래 사진).
문제가 발생하지 않고 운전 속도를 떨어뜨리지 않는 라벨 공급의 자동 교환을 얼마나 원활하게 실현할 수 있는가 하는 기술 과제들을 엿볼 수 있다. 여기에서도 특허를 통해 그 기술의 일부를 소개하겠다.
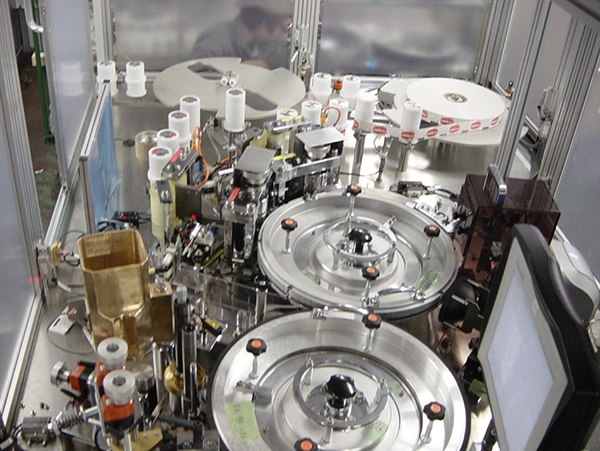
라벨 공급 유닛 방식(특허 1980.6, 특허 1980.7)
라벨 테이블(1)에서 흡인 드럼(5)까지의 공급 장치를 2유닛 설치하고, 제1 유닛의 롤 라벨의 종단을 검지(11)하면 제2 유닛의 운전을 시작하고 제1 유닛은 운전을 정지한다.
당사의 롤 라벨러는 현재까지 이 방식을 채용하고 있다(아래 그림 1장째).
테이프 자동 연결 방식(특허 출원 1982.4)
라벨 테이블(2)을 2유닛 설치하고, 제1 유닛의 롤 라벨이 끝난 것을 검지(R)하면 그 종단부에 제2 유닛의 롤 라벨의 접착제가 붙은 선단부를 압착하여 접합하고 불필요한 부분을 절단(3, 4)하여 라벨 공급을 연속시킨다. 크로네스사(독일) 등이 이 방식을 채용하여 현재에 이른다(아래 그림 2장째).
크로네스사는 당사의 롤 라벨러 개발(1975.7)부터 약 10년 뒤인 1985년에 처음으로 롤 라벨러를 도입했다. 크로네스사의 일본 지사를 개설(1984)한 이듬해의 일이다. 당시 그 라벨 공급 자동 교환 방식은 당사의 라벨 자동 연결 방식(특허 1982.4)과 매우 흡사했다. 또한 라벨 부착 방식으로 그때까지 크로네스사에서 채용하지 않았던 진공흡인식 부착 드럼을 처음으로 채용했다.
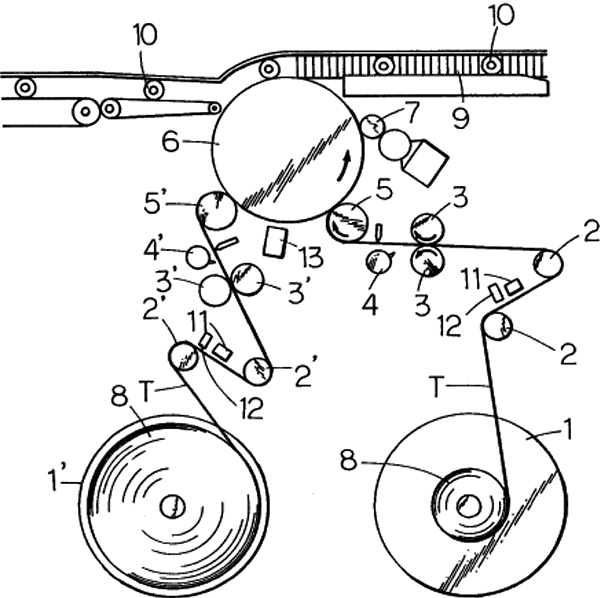
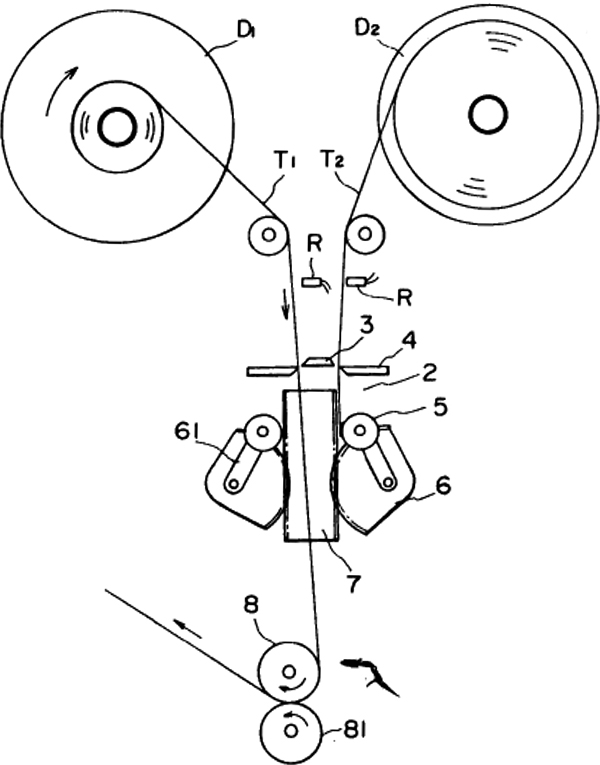
절단 전 라벨 이송 교환 방식(특허 1983.5, 특허 1983.7)
1유닛의 로터리 커터에 대해, 라벨 테이블에서 라벨 공급 롤러까지의 공급 유닛을 2조 갖춘 방식이다.
제1 유닛의 롤 라벨의 종단을 검지하면 제2 유닛의 롤 라벨의 선단과 일치할 때, 제2 유닛의 운전을 시작함과 동시에 제1 유닛의 운전을 정지한다. 롤 라벨의 선단부를 순식간에 후퇴시키는 장치에 의해 롤 라벨의 공급을 자동으로 교환하는 것이다(아래 그림 1장째).
라벨 펀칭기 장착 라벨 공급 유닛 방식(특허 1984.6)
라벨 테이블에서 라벨 펀칭 유닛을 장착한 부착 드럼까지 공급 장치를 2유닛 설치하고, 제1 유닛의 롤 라벨 종단을 검지하면 제2 유닛이 운전을 시작하고 제1 유닛의 운전이 정지하는 방식이다.
롤 라벨이 절단된 경우에도 대기 중인 공급 유닛이 자동으로 운전을 시작하는 것이 특징이다(아래 그림 2장째).
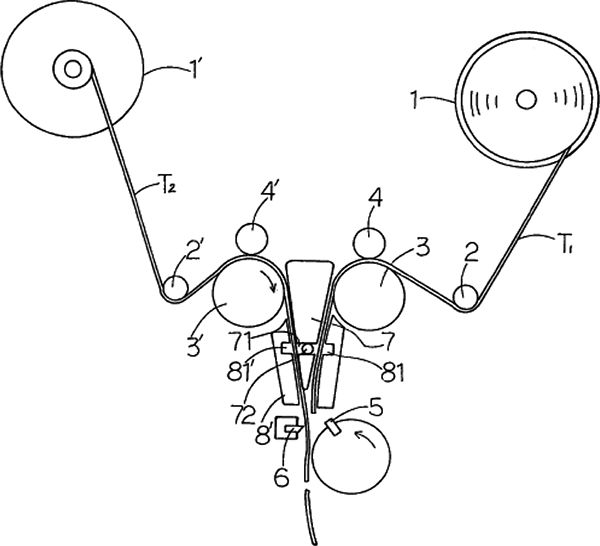
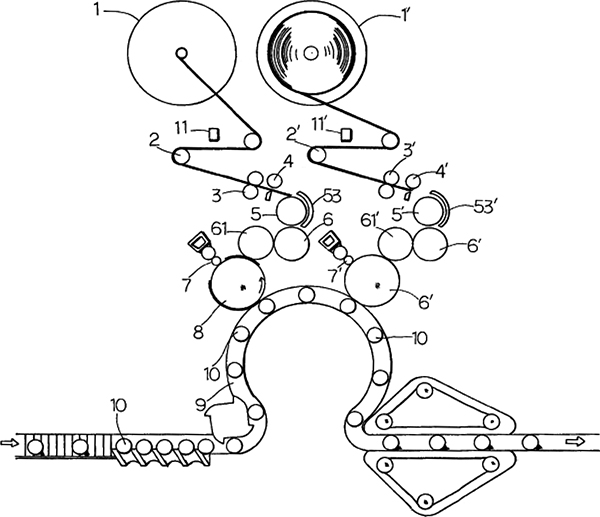
라벨 펀칭 유닛의 도입
롤 라벨에서 부정형 라벨을 연속적으로 펀칭하는 방식의 개발이 1981년부터 1986년까지 진행되어, 펀칭 유닛으로 완성시켰다. 롤 라벨을 로터리 커터에 의해 일정한 속도로 직사각형으로 절단한 후에 펀칭 유닛으로 부정형(타원형 등)으로 펀칭하고 부착 드럼으로 용기에 부착하는 시스템이다.
라벨 펀칭 유닛을 탑재한 롤 라벨러(LR-** P) 1호기가 1984년에 출하됐다.
요동 ‘가위형 절단’식(특허 출원 1981.6)
이 방식은 요동 운동을 통해 커터와 받침 칼날에 의한 ‘가위형 절단’ 효과가 있는 롤 라벨의 펀칭 장치이다. 롤 라벨을 로터리 커터에 의해 직사각형으로 절단하지 않는다.
요철날형(특허 출원 1983.8)(미국·프랑스·영국 특허 1984)
롤 라벨을 로터리 커터에 의해 일정한 속도로 직사각형으로 절단한 후에 펀칭 유닛으로 부정형(타원형 등)으로 펀칭하고 부착 드럼으로 용기에 부착한다. 펀칭하기 전에 라벨을 직사각형으로 절단함으로써 최소 라벨 속도로 펀칭할 수 있다. 펀칭 후 생긴 폐지를 흡인하여 이송한 후 배출 처리하기 때문에 기존의 폐테이프를 감아서 처리하는 회수 장치가 필요 없다(아래 그림 1장째).
절단 후 펀칭식, 라벨 공급 교환 방식(특허 출원 1984.1) (미국, 한국 특허 1985)
위의 (특허 1983.8)의 펀칭 유닛 탑재 롤 라벨러에 라벨 전달 전 라벨 자동 공급 교환 방식(특허 1983.7) 장치를 탑재하여 라벨의 연속 공급을 가능하게 한 것이다.
마찬가지로 천핑 후 생긴 폐지를 흡인하여 이송한 후 배출 처리하기 때문에 기존의 폐테이프 감아서 처리하는 회수 장치가 필요 없다(아래 그림 2장째).
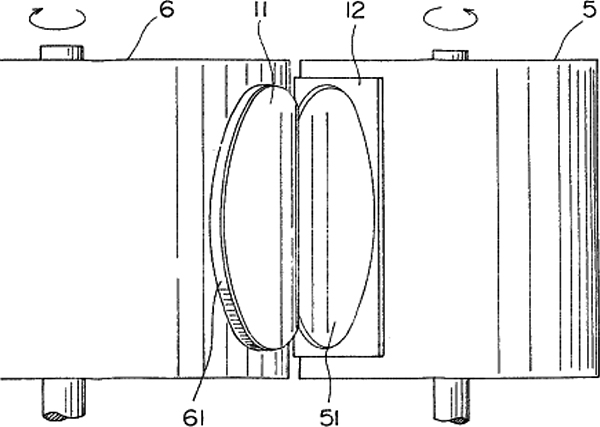
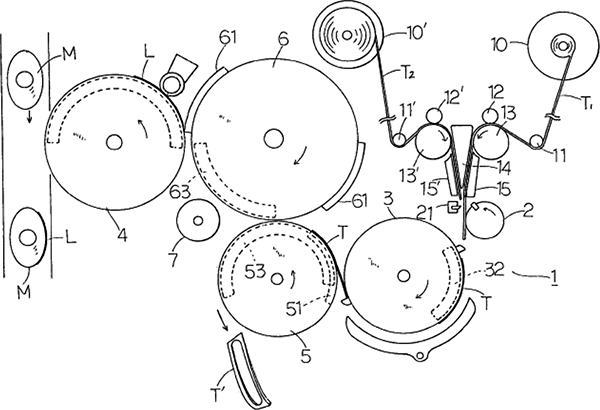
펀칭 라벨의 앞뒤 2점 부착 한쪽 가동 드럼(특허 1985.1)
롤 라벨을 앞뒤 라벨용으로 1장 절단한 후 펀칭 유닛으로 앞뒤 2장 라벨을 펀칭하는 것이다. 부착 드럼부의 슬라이드 흡인 헤드부에서 소정의 거리까지 이동시켜 용기 앞뒤에 라벨을 부착한다.
받침 칼날 드럼 이송식(특허 1986.4) (미국·영국·독일 특허 1987)
롤 라벨을 로터리 커터에 의해 일정한 속도로 직사각형으로 절단한 후에 펀칭 유닛으로 부정형(타원형 등)으로 펀칭하고 부착 드럼으로 용기에 부착한 것이다. 펀칭하기 전에 라벨을 직사각형으로 절단함으로써 최소 라벨 속도로 펀칭할 수 있다.
펀칭 라벨과 폐지를 받침 칼날 드럼으로 이송하여 펀칭 라벨은 부착 드럼으로, 폐지는 배출부로 이송한다. 이 방식은 최종적으로 배치되었다는 것이 앞에서 나온 일련의 특허들과 다른 점이라고 할 수 있다.
펀칭 후 생긴 폐지를 흡인하여 이송한 후 배출 처리하기 때문에 기존의 폐테이프를 감아서 처리하는 회수 장치가 필요 없다(아래 그림).
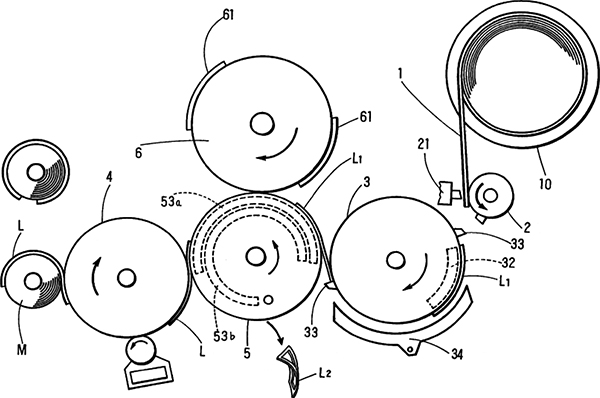
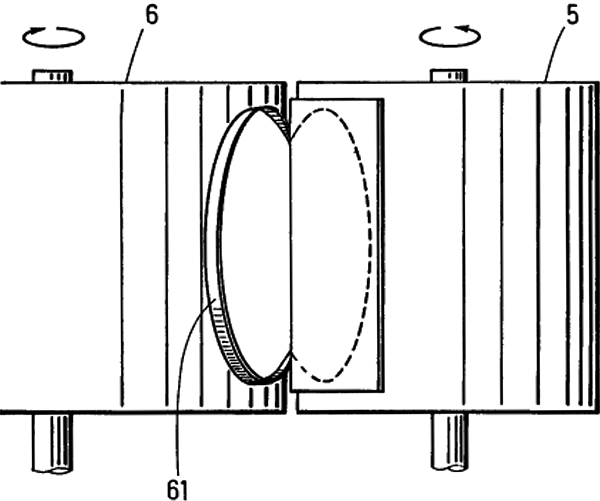
베어링 압력식 최종형(특허 1986.8)
앤빌 드럼과 다이 드럼으로 구성된 펀칭 유닛의 경우 다이 드럼의 베어링부를 숫돌을 장착한 연마 장치로 눌러 다이 커터날이 마모돼도 연속 운전을 가능하게 하는 것이다(아래 그림).
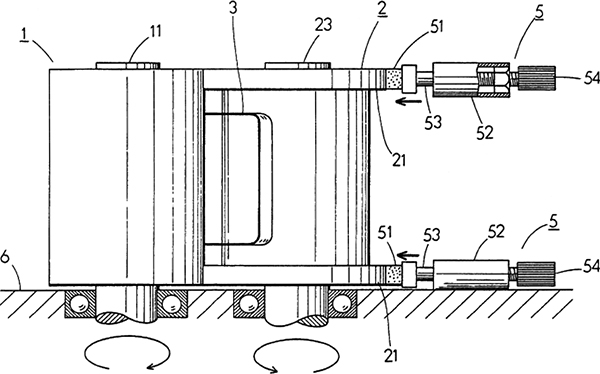
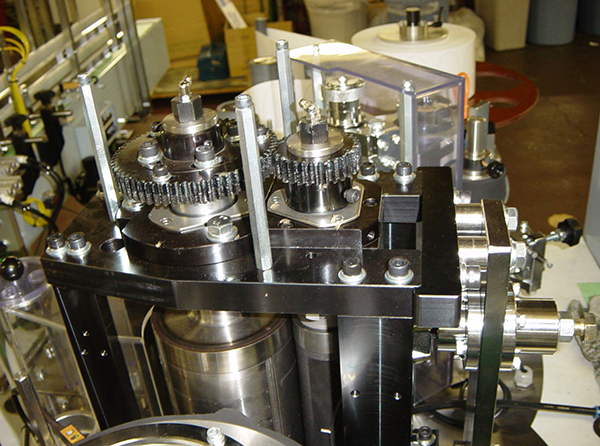
폐지 처리기, 펀칭 유닛의 폐지 압축 처리(특허 1985.1)
라벨 펀칭 유닛에서 발생한 폐지를 2개의 롤러가 회전하면서 끌어들여 압축, 응축시킨다.
롤 라벨 자동 공급 장치 개발
이 장치 개발은 아래와 같은 점에서 꼭 필요했다. 공장 라인에서의 대량 생산에 고속화가 진행되고 있었기 때문에 롤 라벨을 자주 세팅해야 했고 작업자의 부담이 컸다. 복수의 롤 라벨을 적재해두고 거기서 자동으로 롤 라벨을 테이블에 공급하고 테이블에서 공급 롤러를 거쳐 커터까지 자동으로 배치할 수 있다면 작업자는 항상 1대의 라벨러를 감시하지 않아도 되는 것이다.
트레이식 자동 공급 장치(특허 1994.12)
복수의 라벨 롤을 컨베이어(현행은 이송 체인 탑재 적재기로 매단다)상에 적재하여 트레이상에서 전달하고 테이블 위에 넘어트리면서 배치하여, 롤 라벨을 로터리 커터까지 자동으로 정렬한다. 라벨 테이블에 정렬하는 작업을 무인으로 확실하게 할 수 있어 큰 폭의 생력화와 작업 시간 단축을 도모할 수 있는 것이다(아래 그림, 사진).
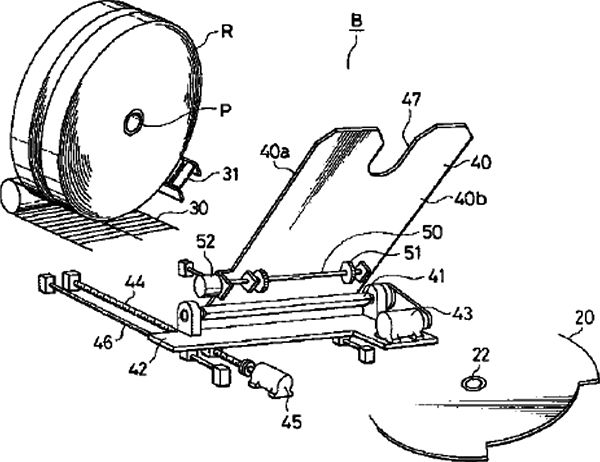
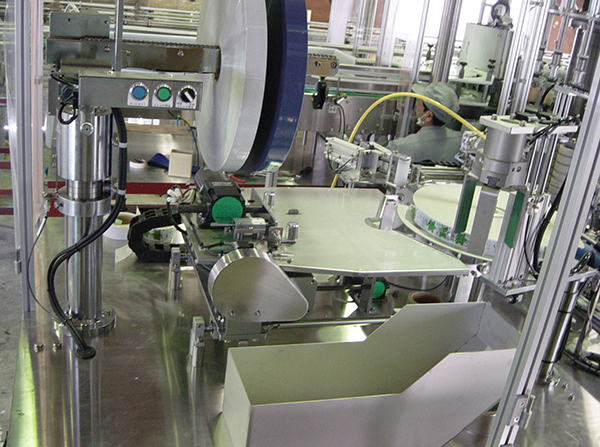
롤 라벨 자동 정렬 장치(특허 1995.7)
이는 고정과 가동 텐션 롤러 2개를 배치하여 라벨을 통과시킨 후에 가동 롤러를 이동시킴으로써 롤 라벨을 자동으로 배치하는 자동 정렬 장치이다.
앞의 롤 라벨 자동 공급 장치와 함께 탑재함으로써 라벨 테이블에 배치하는 것부터 로터리 커터까지 전자동으로 라벨을 정렬할 수 있게 한 것이다(아래 그림, 사진).
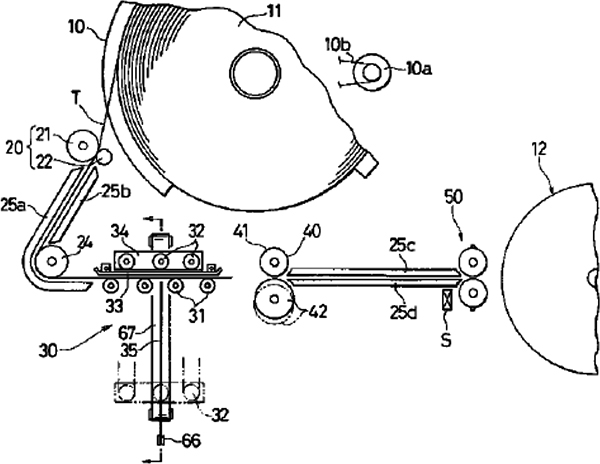
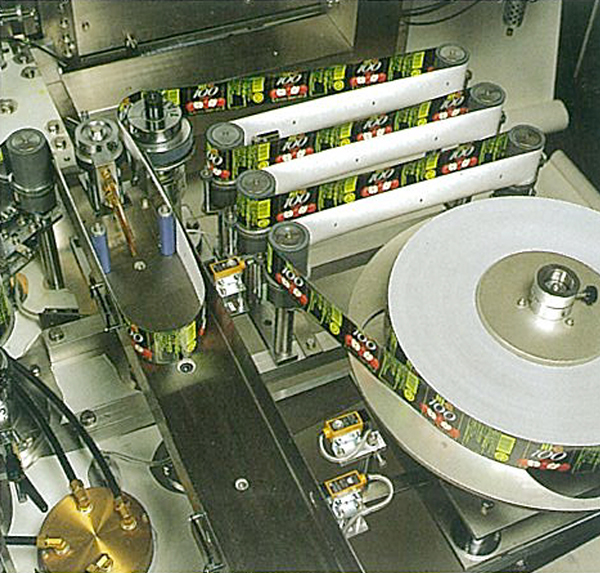
암식 자동 공급 장치(2006.1 실례)
이는 복수의 라벨 롤을 컨베이어상에 적재하고 암식 라벨 정렬 장치가 이를 잡아 눕히면서 라벨 테이블상에 배치하는 자동 공급 장치이다.
라벨 테이블에 배치하는 작업을 무인으로 확실하게 할 수 있어 대폭적인 생력화 및 작업 시간 단축을 도모할 수 있는 것이다(아래 그림, 사진).
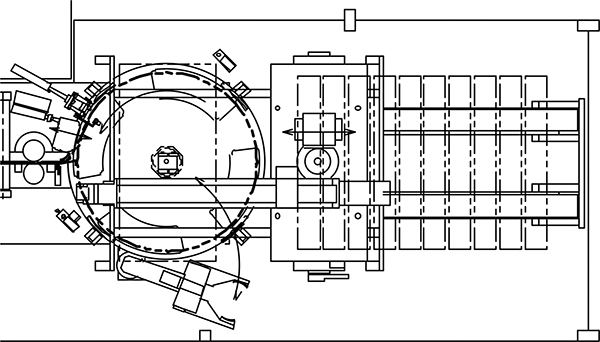
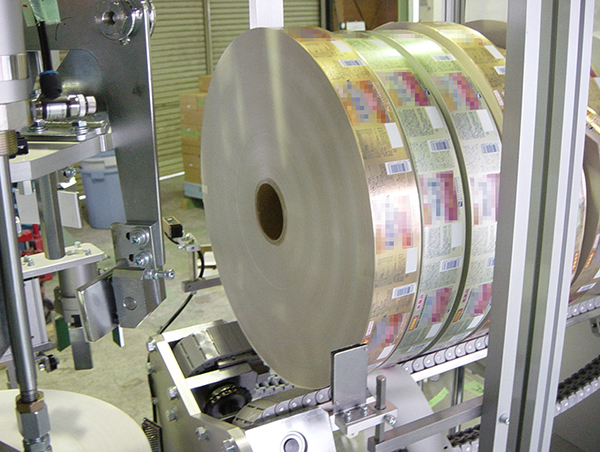
고속 부착 방식
롤 라벨러에서 라벨 이송, 라벨 절단, 커팅 라벨 이송, 라벨 부착, 용기 반송과 같은 일련의 공정이 회전 운동의 연쇄로 진행되고 있다. 이는 기계 운전의 고속화를 추진하는 데 적합한 방식이라고 할 수 있다. 각 장치의 한 가지 성능이 한 단계 좋아지면 이에 따라 다른 장치의 성능 향상에 대한 작업도 진척된다. 그 최종 단계인 라벨 부착 공정에서 용기와 라벨이 만나는 부분의 반송 상태가 이 문제를 해결할 열쇠를 쥐고 있다. 용기가 고속으로 반송됨으로써 생기는 불안정함을 얼마나 극복할 수 있는가가 과제가 된다. 매분 1,000~1,500개에 라벨링 하는 경이로운 속도를 실현한다. 매초 25개라는 반송 속도에 따라 육안으로는 용기의 흐름이 하나의 유동체처럼 보인다.
입구·출구 스타 휠 장착(특허 출원 1985.1)
반송 라인상에서 용기에 라벨을 부착하기 직전 및 직후에 강제적으로 밀고 당기는 작용을 하는 입구 스타 휠 및 출구 스타 휠을 설치하여 용기 속도와 속도를 일정하게 규제함으로써 안정된 속도로 라벨을 부착할 수 있게 했다(아래 그림, 사진).
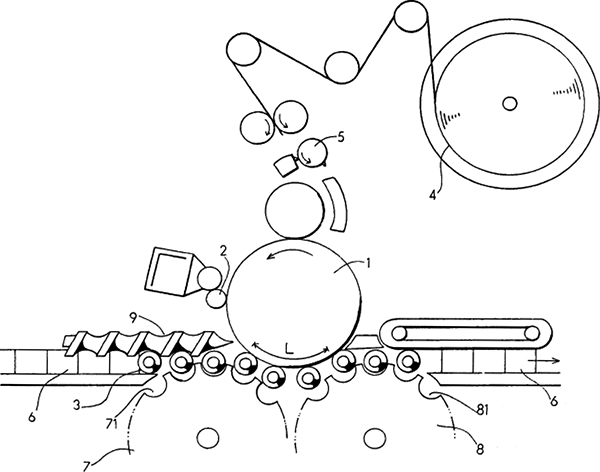
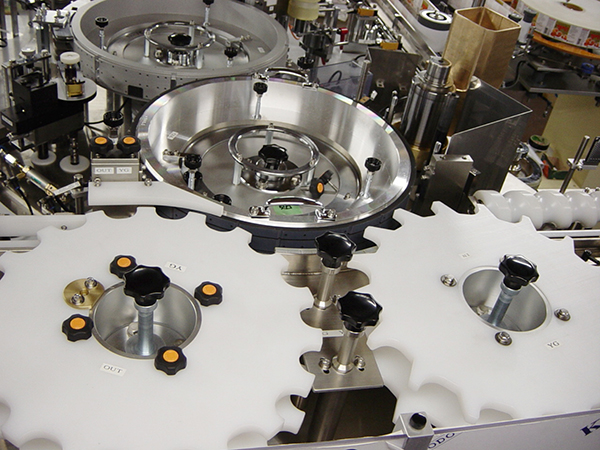
신축 롤러를 장착한 부착 스타 휠(특허 출원 2009.3)
라벨 부착 시에 스타 휠의 신축 2쌍 롤러와 부착 드럼과의 3점에서 용기를 잡아, 롤러의 신축으로 라벨 길이 이상의 부착 드럼의 압착 구간 내에서 라벨 감기(권취), 부착, 마무리를 동시에 고속으로 실현할 수 있게 됐다.
고속기 외에도 바이알 및 앰플 등 작은 직경의 용기에 라벨을 부착할 때도 유효한 방식이며, 스티커 라벨러(LKS형)에도 탑재되어 있다(아래 그림, 사진).
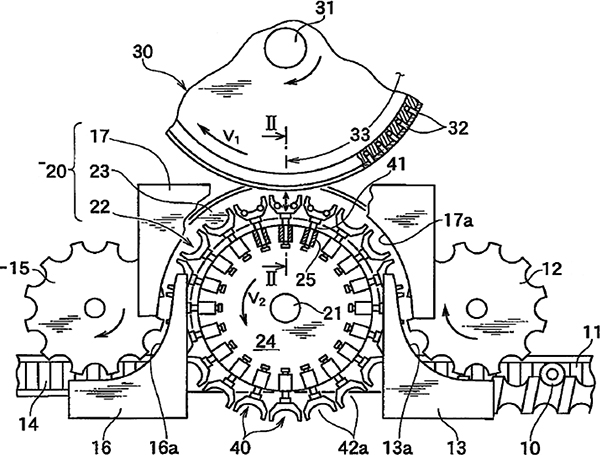
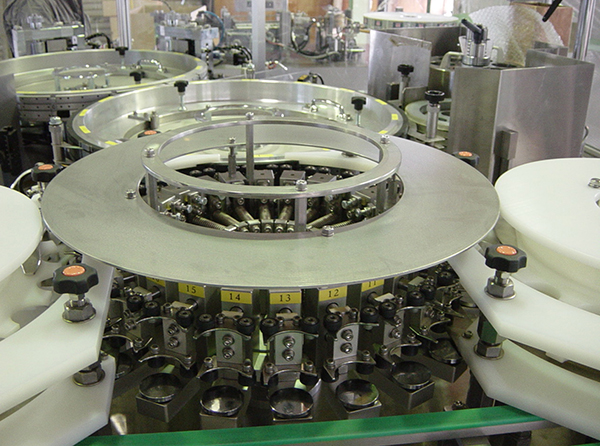